Du minerai à l'acier brut : un voyage fascinant dans le monde de la métallurgie
Matière Expertise
Il y a longtemps, un groupe de chasseurs-cueilleurs s'installa dans les montagnes. Un jour, ils tombèrent sur une étrange pierre, lourde et brillante à la lumière du soleil. Ils l'ont emportée au camp et ont vite compris sa valeur. Le minerai a été extrait et traité, donnant naissance à des outils, des armes ainsi que des œuvres d'art. Aujourd'hui, il est impossible d'imaginer notre société sans ce métal précieux.

Spécialiste en marketing
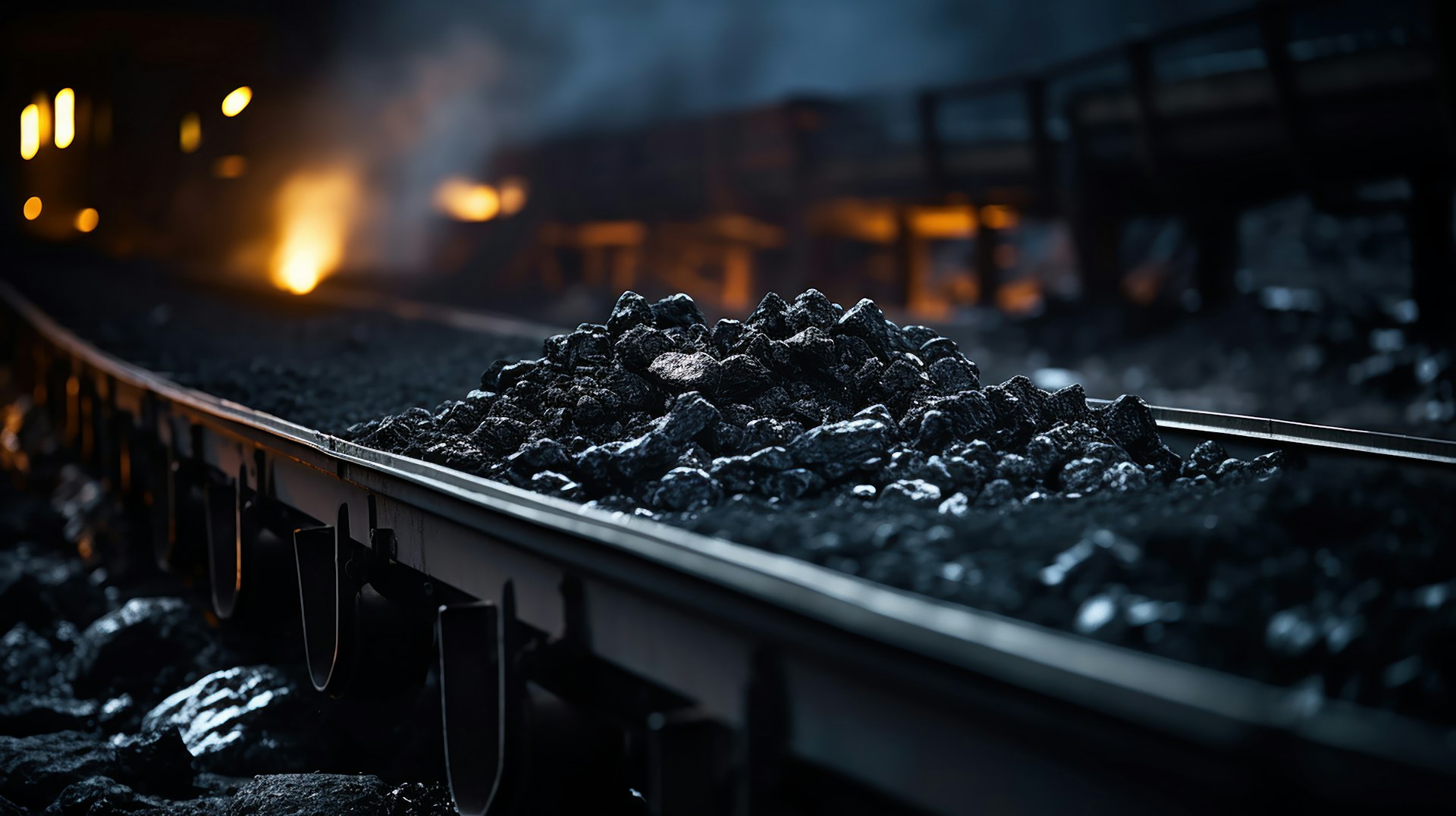
Extraction de minerais : aperçu des types de gisements de minerais
La plupart des métaux, dont le fer, ne sont pas nobles. Ils n'existent pas à l'état pur dans la nature, mais sous forme de composés chimiques avec de l'oxygène, du soufre et d'autres matières non métalliques. Seuls les métaux précieux, comme l'or, se trouvent sous forme de métal noble.
L'extraction du minerai est la première étape du long processus de fabrication de l'acier. Pour obtenir le précieux minerai, différents types de gisements doivent être identifiés et exploités. Les principaux types de minerai de fer sont :
la magnétite Fe3O4 (pierre de fer magnétique)
l’hématite Fe2O3 (pierre de fer rouge)
la limonite FeO(OH) (pierre de fer brune)
la sidérite FeCO3 (spath de fer)
la pyrite FeS2 (pyrite de fer)
Chaque gisement de minerai a ses propres caractéristiques et nécessite des méthodes d'exploitation minière et d'extraction spécifiques.
Types d’extraction de minerais
Dans l'exploitation minière, différentes techniques sont disponibles pour extraire le minerai de la terre.
Parmi les techniques les plus courantes, on trouve:

L'exploitation à ciel ouvert
L'exploitation à ciel ouvert est un terme utilisé dans l'industrie minière. Il se réfère à l'extraction de ressources minérales dans des zones proches de la surface. En plus de la composante technologique, l'exploitation à ciel ouvert désigne l'installation ou le site sur lequel cette technique est appliquée.
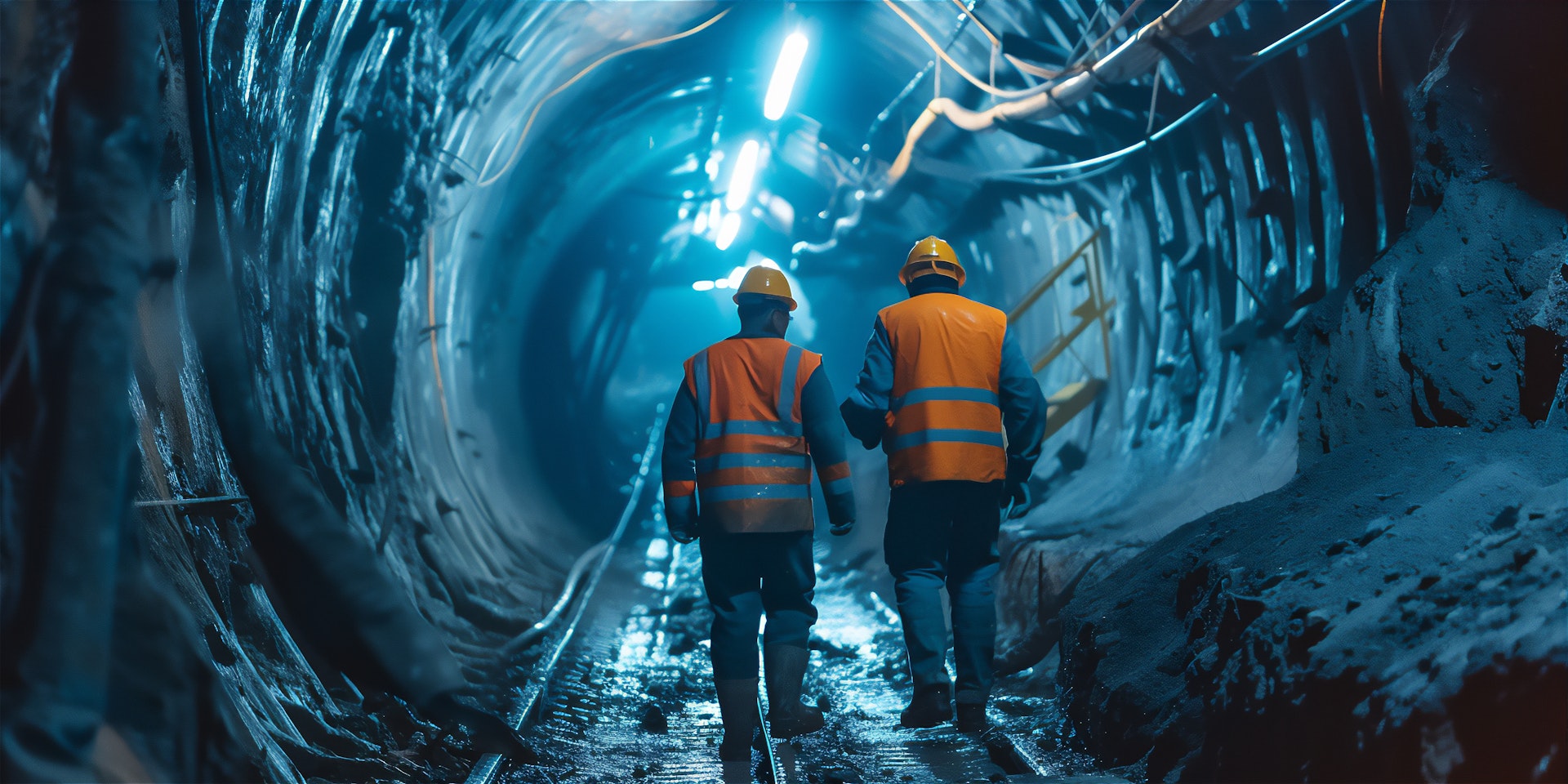
L’exploitation souterraine
L'exploitation minière souterraine désigne la création de cavités sous la surface de la terre, c'est-à-dire dans la roche, sous terre. L'exploitation minière souterraine permet d'exploiter des ressources minérales qui se trouvent dans des gisements plus profonds.
L'importance des installations de frittage
Sur le chemin de la production d'acier, il y a un élément crucial qui reste souvent dans l'ombre des hauts fourneaux incandescents et des impressionnantes aciéries : l'installation de frittage. Pourtant, cette installation apparemment modeste joue un rôle clé dans le prétraitement des minerais de fer et a un impact énorme sur la qualité et l'efficacité du processus de haut fourneau.
Une installation de frittage est un équipement spécialisé qui sert à transformer les minerais de fer en un matériau poreux et solide appelé "sinter". Ce processus d'agglomération ou de solidification des minerais est essentiel, car il prépare les minerais à être utilisés dans les hauts fourneaux.
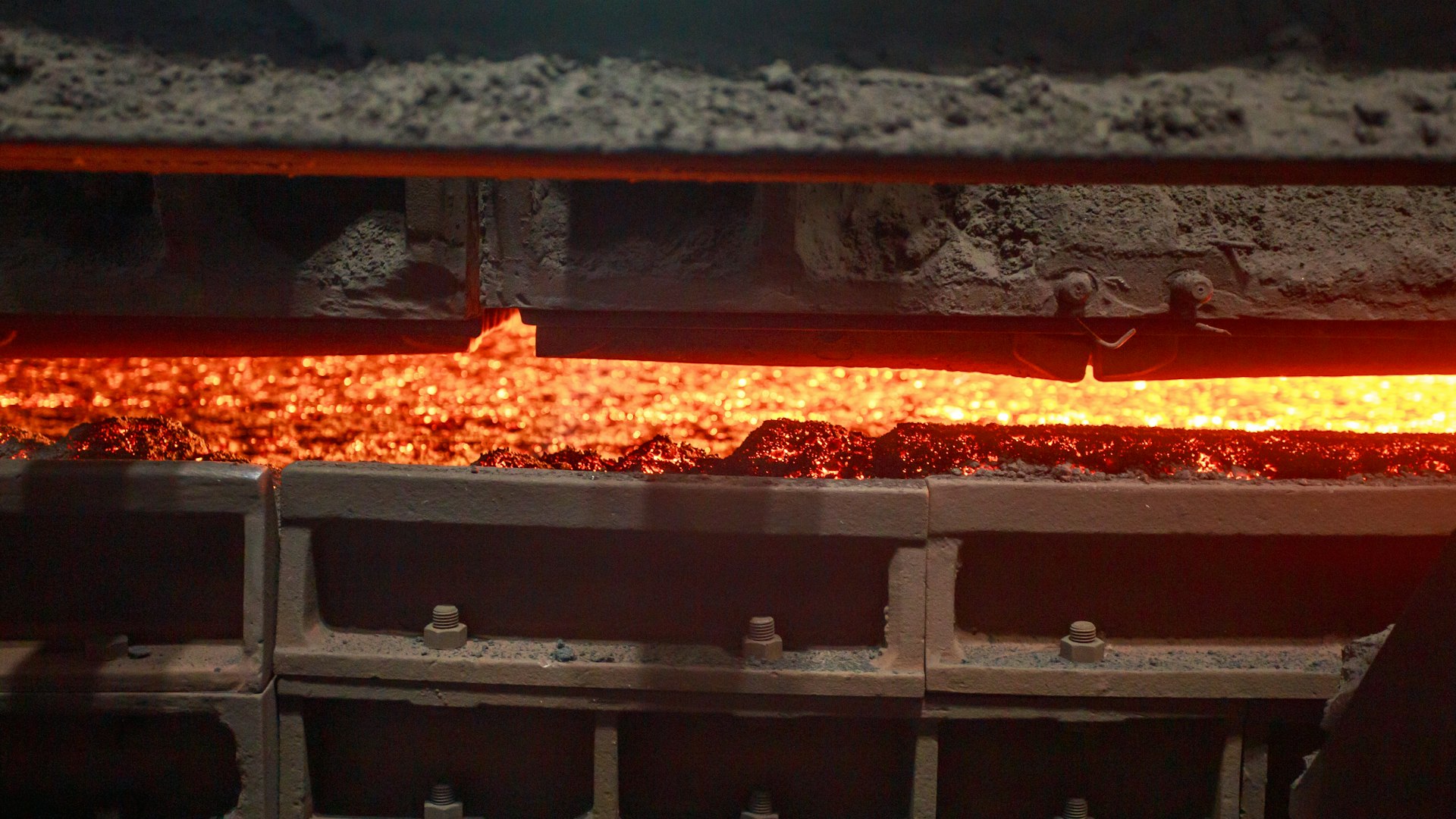
Que se passe-t-il lors du procès :
Prétraitement du minerai : les minerais de fer extraits des mines sont rarement sous une forme pouvant être utilisée directement dans les hauts fourneaux. Ils contiennent souvent des impuretés et ont une granulométrie trop fine pour être fondus efficacement. C'est là qu'intervient l'installation de frittage. Elle chauffe les minerais à haute température et les amène à s'agglomérer, ce qui les transforme en un produit fritté adapté aux hauts fourneaux.
Amélioration de la qualité des matières premières : le processus de frittage permet non seulement d'éliminer certaines impuretés, mais aussi de mélanger différents types de minerais. Cela permet d'améliorer considérablement l'homogénéité et la qualité de la matière première.
Amélioration de l'efficacité : le frittage est poreux et permet une répartition uniforme de la chaleur et des gaz de réduction dans les hauts fourneaux. Il en résulte une combustion et une fusion plus efficaces, ce qui réduit au final la consommation d'énergie et augmente la productivité.
Impact sur l'environnement : l'utilisation d'installations de frittage réduit également l'impact sur l'environnement, car moins de matières premières et d'énergie sont nécessaires pour produire un acier de haute qualité. Cela contribue à la durabilité de la production d'acier.
Après avoir subi le processus d'agglomération décisif dans l'installation de frittage, les minerais de fer sont maintenant prêts pour la prochaine phase de leur voyage – le voyage vers le cœur de la production d'acier, le haut fourneau.
Le haut-fourneau et la fabrication de la fonte
Faits sur le haut fourneau
Les hauts fourneaux sont généralement exploités sans interruption pendant environ 10 à 15 ans. Après cette période, appelée "voyage du four", une révision importante du haut fourneau est nécessaire.
Les hauts fourneaux moyens atteignent des rendements journaliers de 6000 tonnes, les grands hauts fourneaux jusqu'à 13 000 tonnes de fonte.
Le haut fourneau habituel a généralement une hauteur d'environ 25 à 30 mètres.
Le four est constitué de briques réfractaires entourées d'une enveloppe en acier.
La paroi extérieure d'un haut fourneau est refroidie en permanence par des circuits de refroidissement fermés.
Matières premières nécessaires à la production de fonte brute :
minerais de fer
coke
charbon
pétrole
gaz
chaux
air et oxygène pur
Dans le processus du haut fourneau, le minerai de fer, les granulats et le coke sont introduits par le haut dans le haut fourneau. La chaleur dans le haut fourneau fait que le coke fixe l'oxygène et que les impuretés indésirables sont partiellement évacuées par le laitier.
Pour maintenir le processus du haut fourneau, l'introduction d'air chaud, appelé "vent", se fait dans la partie inférieure du four. Avant que le vent ne soit injecté dans le four, un préchauffage a lieu dans les réchauffeurs de vent (cowper) afin d'atteindre la température de fonctionnement souhaitée.
Bilan matière pour la production de 12 000 tonnes de fonte. Cela correspond à la production quotidienne moyenne d'un haut fourneau moderne.
Alimentation des hauts fourneaux :
Matériau | Poid |
---|---|
Minerai et agrégats | 19 200 tonnes |
Coke | 3600 tonnes |
Charbon | 2160 tonnes |
Vent chaud | 10.8 millions m³ |
Oxygène | 1.2 millions m³t |
Sont prélevés :
Matériau | Poid |
---|---|
Fonte brute | 12 000 tonnes |
Scories | 3120 tonnes |
Gaz de haut fourneau | 16.8 millions m³ |
Poussière | 12 tonnes |
Lors de la coulée du haut fourneau, le contenu en fusion du four est retiré par une ouverture fermée dans la partie inférieure. Dans la halle de coulée, le contenu sortant est séparé en scories et en fer liquide à l'aide d'un système de rigoles. La plupart des hauts fourneaux disposent de deux dispositifs de coulée distincts : l'un pour les scories et l'autre, situé un peu plus bas, pour la fonte liquide. La différence de densité est utilisée pour permettre une séparation efficace.
Le laitier est un mélange de différents oxydes tels que l'oxyde de silicium (acide silicique, silicate), l'oxyde de calcium, l'oxyde de magnésium, l'oxyde d'aluminium (alumine) et autres. En général, on les décrit de manière simplifiée comme du silicate de calcium et d'aluminium. Ces scories sont souvent utilisées sous forme de particules grossières ou de laitier granulé et sont également utilisées dans l'ingénierie. Les scories siliceuses sont également transformées en laine de roche et en laine de laitier.
Du haut-fourneau à l'aciérie
La fonte obtenue dans le haut-fourneau est encore loin d'être un acier techniquement utilisable. La fonte contient 4 à 4,7 % de carbone et d'autres éléments réduits comme le soufre, le phosphore, le silicium et le manganèse.
Après la coulée, la fonte est versée dans des bacs à torpilles et acheminée vers l'aciérie par le réseau ferroviaire de l'usine. La fonte y est transformée en acier dans des convertisseurs (conversion). Les impuretés telles que le soufre, le phosphore, le silicium, le carbone et le manganèse, qui accompagnent le fer, sont en grande partie éliminées.
De la fonte brute à l'acier brut
Le traitement de la fonte est une étape décisive du processus de fabrication de l'acier. Il commence en partie déjà dans la poche torpille par une désulfuration.
Les principaux processus dans le convertisseur jusqu'à l'acier brut sont décrits plus en détail ci-dessous.
Désulfuration : le soufre est une impureté présente dans la fonte qui peut nuire à la qualité du produit final. Pour éliminer le soufre, un agent de désulfuration tel que le carbure de calcium, le magnésium ou le carbonate de sodium (soude) est injecté dans la poche torpille. Ces matériaux réagissent avec le soufre présent dans la fonte et forment des scories qui sont plus légères que le fer liquide et peuvent donc être séparées. La désulfuration améliore la soudabilité et les propriétés mécaniques de l'acier qui sera produit par la suite.
Déphosphoration : le phosphore est une autre impureté qui doit être éliminée de la fonte, car des teneurs élevées en phosphore peuvent nuire à la qualité de l'acier. Des flux calcaires contenant de l'oxyde de calcium (chaux) sont ajoutés pour lier le phosphore dans la fonte sous forme de laitier phosphoré. Ce laitier remonte à la surface de la fonte liquide et peut être facilement écumé.
Désiliciation : le silicium est une impureté qui peut être présente dans la fonte brute et qui peut affecter la soudabilité et la résistance mécanique de l'acier. De l'oxyde de fer ou d'autres agents réducteurs de silicium sont ajoutés afin d'oxyder le silicium et de le transférer dans le laitier. Cela facilite l'élimination du silicium du fer liquide.
Décarburation : le carbone est brûlé par injection d'oxygène pur. Lors de ce processus connu sous le nom d'«affinage», le métal en fusion s'échauffe fortement et rapidement (réaction exothermique). Pour éviter un échauffement excessif, on utilise de la ferraille d'acier pour le refroidissement.
Désoxydation : l'affinage augmente la teneur en oxygène dans la masse fondue, ce qui n'est pas non plus souhaitable. Celui-ci est à nouveau lié par désoxydation avec du silicium ou de l'aluminium et évacué par le biais des scories.
Le traitement de la fonte nécessite un contrôle et une surveillance précis afin de s'assurer que les impuretés sont réduites au niveau souhaité.
A la fin du traitement de la fonte dans le convertisseur, on obtient des lots d'acier brut avec des teneurs définies en carbone, silicium, manganèse, soufre, phosphore et oxygène.
L'acier brut est alors traité et allié par d'autres processus métallurgiques de manière à obtenir un acier de composition chimique définie et présentant le profil de propriétés souhaité.
Il est important de souligner que l'acier brut n'est pas identique à l'acier inoxydable. L'acier brut sert de matériau de base et doit être soumis à des étapes de transformation supplémentaires. L'acier inoxydable contient au moins 10,5 % de chrome (Cr) et jusqu'à 1,2 % de carbone (C).
Lisez aussi notre blog "La révolution de l'acier inoxydable - un voyage fascinant dans l'univers de l'acier inoxydable"
Le raccordement de l'acier brut à l'acier inoxydable se fait par l'ajout des éléments d'alliage décrits et par des procédés de traitement spéciaux qui affinent l'acier.
Conclusions
Dans cette exploration du processus de fabrication de l'acier brut, nous avons eu un aperçu du monde de la métallurgie. De l'extraction des minerais à leur transformation en acier brut, nous avons mis en lumière les étapes et les technologies complexes qui se cachent derrière cette industrie vitale. Nous avons vu comment les procédés et les technologies les plus modernes contribuent à améliorer constamment la qualité et l'efficacité de la production d'acier.
En conclusion, nous pouvons affirmer que l'acier est plus qu'un simple matériau de construction. C'est un symbole de progrès, d'innovation et de la capacité de l'homme à façonner son environnement.
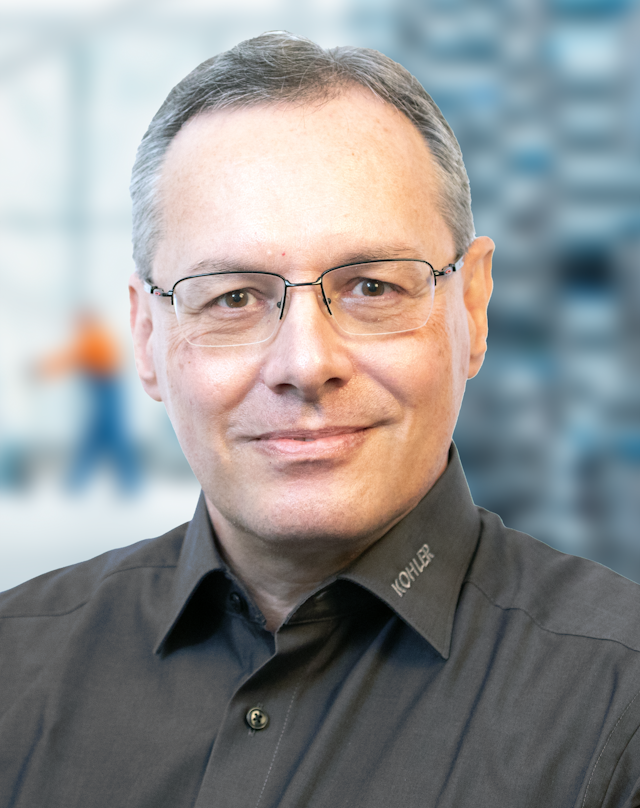
Avez-vous des questions? Je vous conseille volontiers personnellement!
Contact
Dr. René Mächler
Responsable technique et assurance qualité / Ingénieur en matériaux diplômé EPF
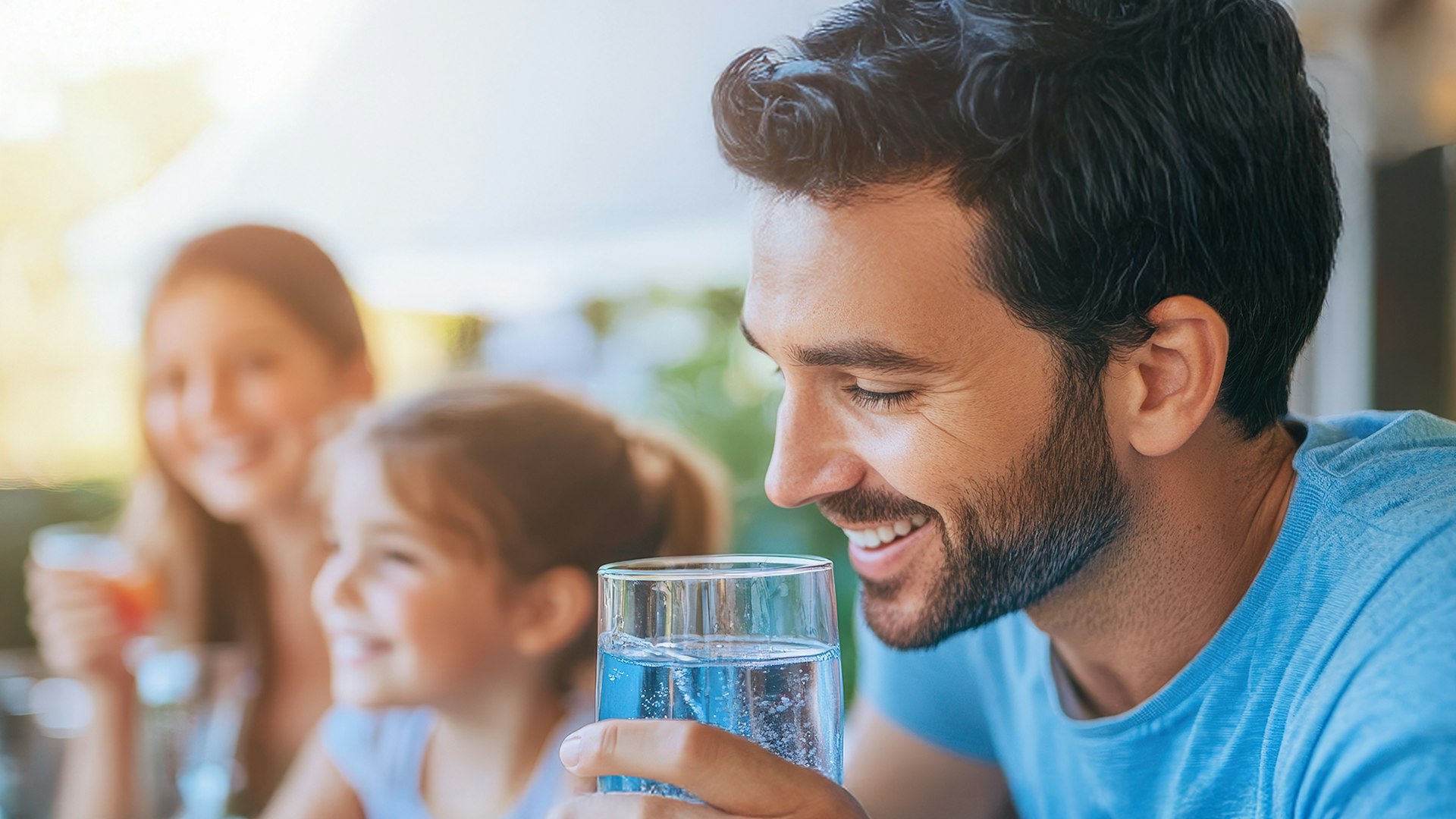
- Expertise
- Exemples d'application
- Refrences
- Consultation
Tout sur le projet d'extension "ARA Basel" (STEP de Bâle) pour l’amélioration du traitement des eaux usées
Les stations d'épuration des eaux usées et l'acier inoxydable sont une combinaison indispensable pour fournir de l'eau potable de haute qualité à la population.

Des partenariats porteurs de sens : KOHLER encourage le sport, l'innovation et la science
KOHLER attache une grande importance à la promotion d'activités significatives et à son positionnement en tant qu'acteur actif au sein d'un réseau engagé.
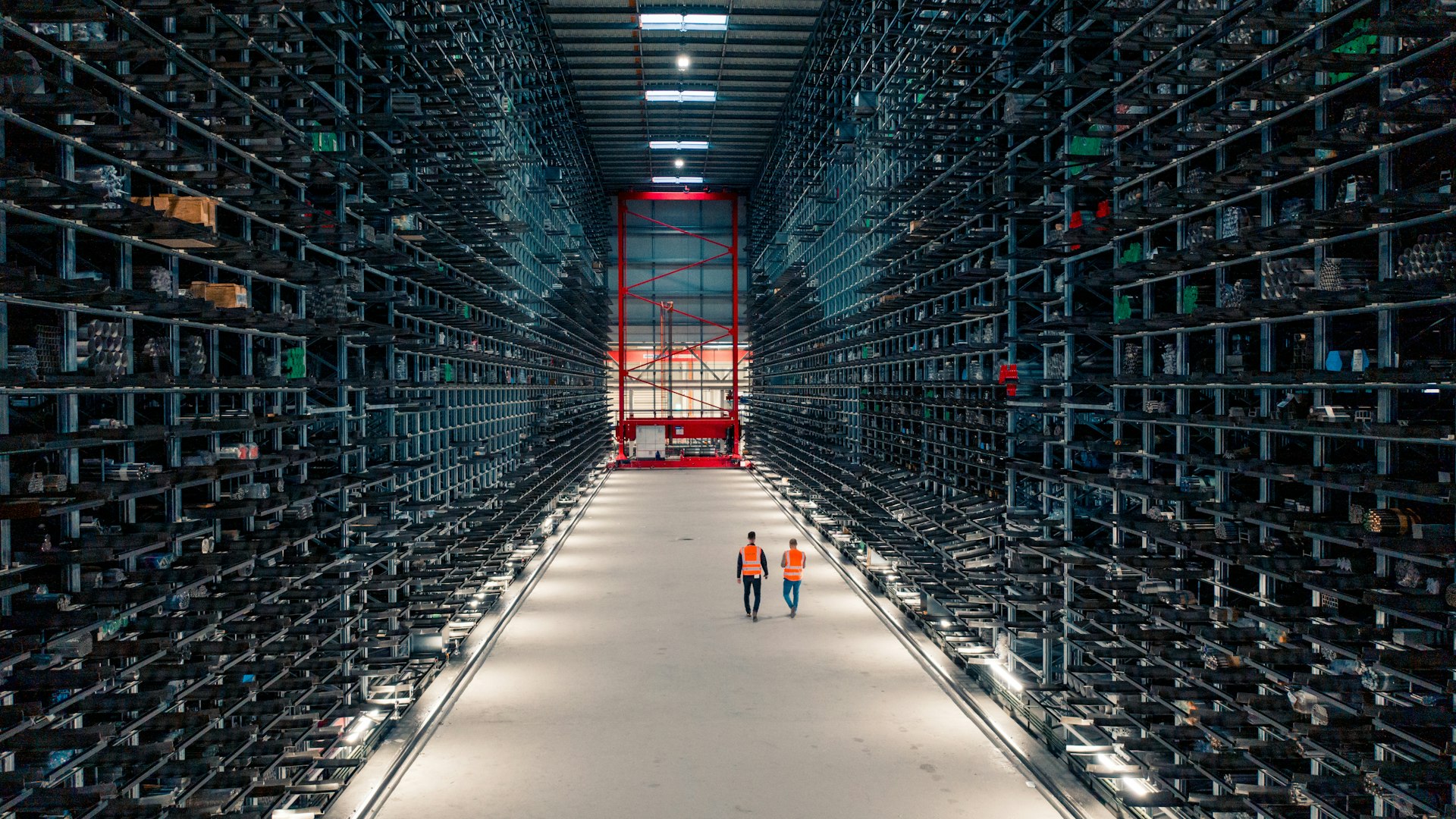
HANS KOHLER SA - Votre N° 1 pour les aciers inoxydables
HANS KOHLER SA est une entreprise commerciale autonome et indépendante dont le siège est à Zurich.