Chemische und elektrochemische Oberflächenbehandlungen von Edelstahl. Eine kurze Einführung.
Fachwissen Werkstoff Beratung
Edelstahl ist ein vielseitiger Werkstoff, der aufgrund seiner Korrosionsbeständigkeit, mechanischen Eigenschaften und Ästhetik in einer breiten Palette von Anwendungen eingesetzt wird. Um die Leistungsfähigkeit und Langlebigkeit von Edelstahl weiter zu verbessern, kommen chemische und elektrochemische Oberflächenbehandlungen zum Einsatz. In diesem Blogbeitrag werfen wir einen Blick auf die verschiedenen Varianten dieser Behandlungen und ihre jeweiligen Vorteile.

CEO
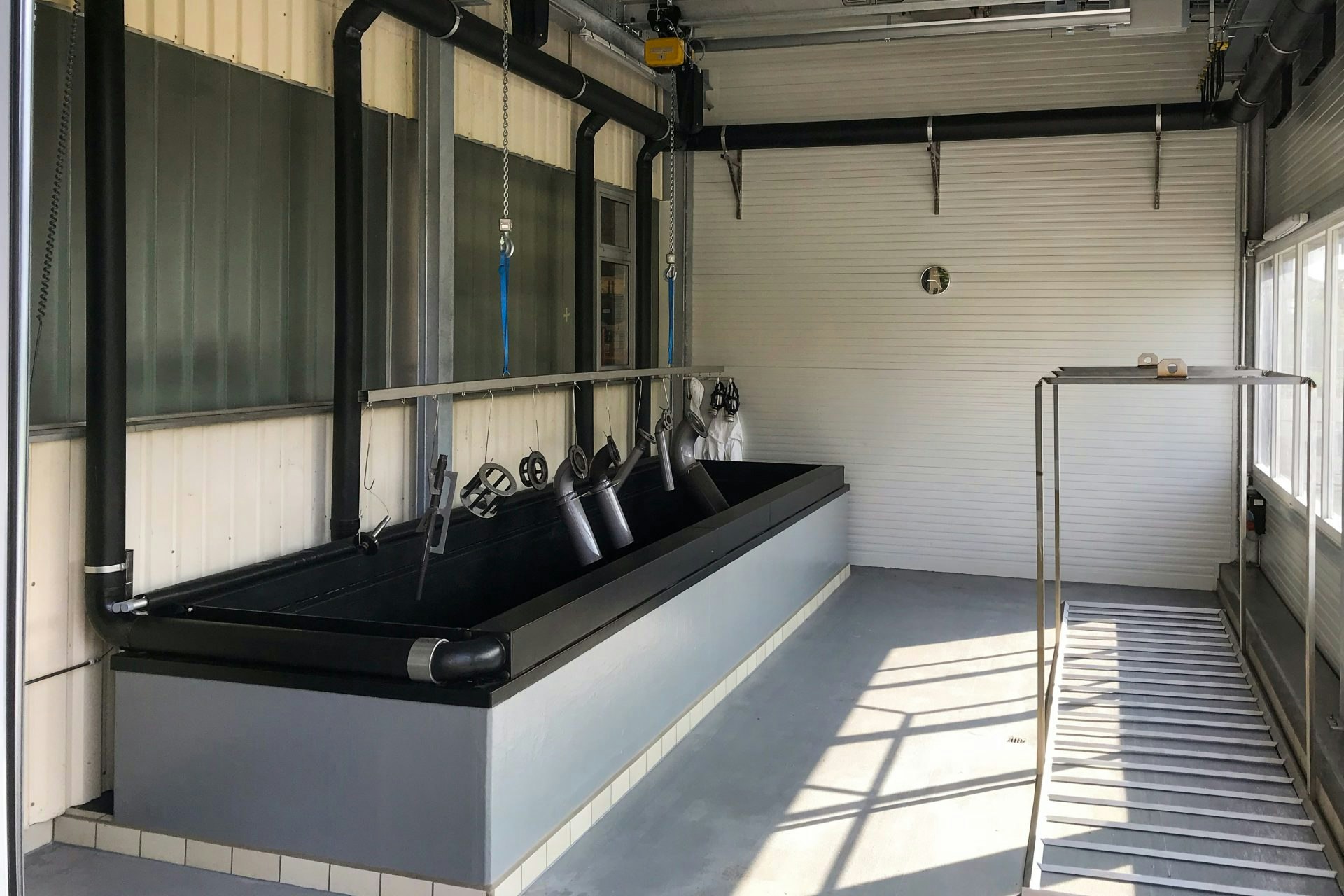
Die Beizbehandlung als wichtigste chemische Oberflächenbehandlungen
Die Beizbehandlung gilt als die bedeutendste chemische Oberflächenbehandlung für nichtrostenden Stahl. Sie zielt darauf ab, eine kontrollierte allgemeine Korrosion, sprich Ätzung, des nichtrostenden Stahls zu bewirken. Das Hauptziel besteht darin, den Oxidfilm sowie die darunterliegende entchromte Schicht zu entfernen, die die Korrosionsbeständigkeit erheblich beeinträchtigen könnten. Durch das Beizen werden auch effektiv Sulfide, Phosphide und Einschlüsse entfernt, was die korrosionstechnischen Schwächen verringert.
Der Beizprozess umfasst normalerweise vier Schritte:
Gründliche Entfettung des Werkstücks, oft mit verdünnter Lauge wie Natriumhydroxid (NaOH)
Beizen in einem Bad oder mit einer Paste bzw. einem Spray
Sorgfältiges Spülen mit reinem Wasser, gefolgt von einem Nachspülen mit demineralisiertem Wasser, um Kalkflecken zu vermeiden
Trocknen an der Luft oder mit Druckluft, um Fleckenbildung zu minimieren
Der Beizprozess erfolgt durch das Tauchen oder Baden des Werkstücks in der Beize. Die Beize besteht aus etwa 10 bis 20 % Salpetersäure (HNO3) mit einem Aktivator, um die schützende Chromoxidschicht anzugreifen. Oft werden Flusssäure (HF) oder andere Fluoridprodukte wie Ammoniumbifluorid (NH4HF2) zugesetzt. Nach dem Beizen ist gründliches Spülen mit reinem Wasser und Nachspülen mit demineralisiertem Wasser erforderlich. In den meisten Fällen ist keine sofortige Passivierung notwendig, da der Stahl in einer leicht feuchten Umgebung von selbst repassiviert wird.
Es ist wichtig zu beachten, dass nicht alle Arten von nichtrostenden Stählen für das Beizen geeignet sind, u.a. sind dies:
Martensitischer Messerstahl
Niedriglegierte ferritische Stähle
Schwefellegierter Automatenstahl
Diese Stähle erfordern besondere Vorsichtsmassnahmen.
Folgende Stähle sind für das Beizen geeignet:
Austenitische nichtrostende Stähle
Nichtrostende Duplexstähle
Einige ferritische nichtrostende Stahllegierungen
Ein erfolgreich gebeiztes Werkstück weist eine satinartige Oberfläche auf, die auf das Ätzen des Stahls zurückzuführen ist und eine erhöhte Oberflächenrauigkeit bewirkt.
Im folgenden Teil wird dargestellt, wie die Beizbehandlung stattfindet.
Was für Vorteile und Nachteile bietet die Beizbehandlung?
Die Beizbehandlung wird am einfachsten durch das Eintauchen des gesamten Werkstücks in ein Beizbad durchgeführt. Anschliessend wird das Werkstück gründlich mit reinem Wasser abgespült.
Badbeize bietet u.a. folgende Vorteile:
Besonders für kleine bis mittelgrosse Werkstücke geeignet
Schneller Prozess
Einfache Anwendung
Umwälzung ist einfach möglich
Einfache Temperatursteuerung
Das Beizbad kann durch Zugabe neuer Säure regeneriert werden.
Durch die Umwälz- oder Berieselungsbeize können fertig montierte Tank- und Rohrleitungssysteme gebeizt werden.
Durch Sprüh- oder Pastenbeizen können besonders grosse Werkstücke oder Stellen, die nicht vollständig gebeizt werden sollen, bearbeitet werden; dabei wird dickflüssiges Beizmittel aufgetragen, entweder mit einer Niederdruckspritze oder einem säurebeständigen Pinsel.
Allerdings hat die Badbeize auch Nachteile:
Begrenzte Werkstückgrösse
Begrenzte Anpassungsfähigkeit des Bads
Hohe Anlagenkosten
Umfassende Sicherheitsvorkehrungen müssen getroffen werden
Aufwendige Entsorgungsprozesse für die Beize
Im folgenden Teil werden einige Tipps bei für das Beizen gegeben:
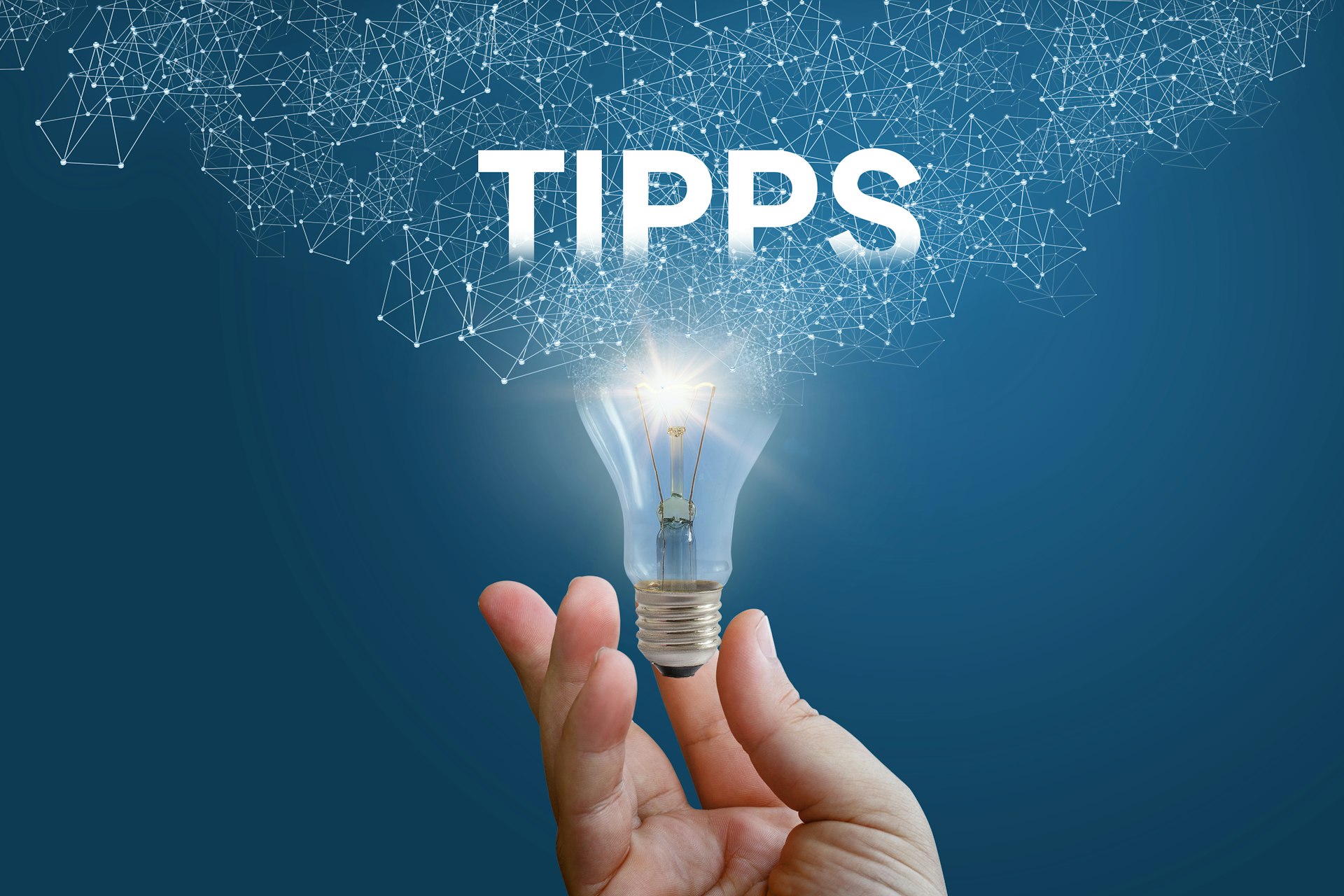
Auf was muss beim Beizen geachtet werden?
Das Beizen von nichtrostendem Stahl mag auf den ersten Blick einfach erscheinen, birgt jedoch eine Vielzahl von Möglichkeiten für Fehler und Herausforderungen:
Es ist wichtig zu beachten, dass nicht jedes Werkstück aus nichtrostendem Stahl gebeizt werden kann. Selbst wenn der Stahl unproblematisch ist, dürfen bestimmte Gummidichtungen, wie zum Beispiel EPDM, nicht mit der stark oxidierenden Salpetersäure in Kontakt kommen. Dies kann insbesondere bei grossen Rohrleitungssystemen mit vielen Dichtungen zu Einschränkungen führen.
Die Vorbereitung, wie das vorherige Entfetten, ist ebenfalls bedeutsam. Dies erfolgt oft chemisch, etwa mit einer verdünnten Lauge oder alkalischen Produkten mit Detergenzien. Eine unzureichende Entfettung kann zu einem ungleichmässigen und fleckigen Aussehen führen.
Der Beizprozess selbst ist komplex, da es sich um einen kontrollierten Korrosionsprozess handelt, bei dem das gewünschte Ergebnis nicht immer leicht zu erreichen ist. Besonders herausfordernd ist die Erzeugung einer gewünschten Oberflächenrauheit. Die Konzentration der Flusssäure sowie die Beizzeit beeinflussen die Rauheit.
Nach dem Beizprozess ist die Oberflächenrauheit bei verschiedenen Stahlsorten unterschiedlich. Ferritische Stähle sind generell weniger beständig gegenüber starken Säuren als austenitische Stähle. Beim nichtrostenden Stahl der Sorte 1.4509 ist die Korrosionsgeschwindigkeit und die endgültige Oberflächenrauigkeit grösser als bei den Sorten 1.4307 und 1.4404.
In der Praxis ist es oft erforderlich, bestimmte Toleranzgrenzen für die Oberflächenrauheit einzuhalten, besonders in Branchen wie Brauereien, Molkereien und Pharmawerken.
Des Weiteren gilt zu beachten, dass frische Säure im Beizbad bedeutend aggressiver ist als gebrauchte Beizsäure.
Des Weiteren kann das Erscheinungsbild des Werkstücks zu Fehlinterpretationen führen. Das Entfernen von Oxidfilm kann zu optischen Effekten führen. Je nach Lichteinfall können die Zonen dunkler oder heller aussehen, was die Vermutung zulässt, dass das Produkt nicht richtig gebeizt wurde.
Der Spülprozess nach dem Beizen kann ebenfalls knifflig sein, besonders bei grösseren Flächen. Normalerweise wird ein Spülbad in Kombination mit einem Wasserschlauch verwendet. Das Erzielen eines einheitlichen Ergebnisses, insbesondere aufgrund der Oberflächenrauheit, ist eine grosse Herausforderung.
Bei grösseren Systemen kann das vollständige Entfernen der Säure schwierig sein. Beispielsweise bei Heizmänteln muss eine vollständige Entleerung sichergestellt sein, andernfalls besteht die Gefahr, dass Beizsäure aus dem Produkt sickert.
Wie dargestellt zeigt sich, dass das Beizen von nichtrostendem Stahl trotz seiner vermeintlichen Einfachheit eine Reihe von Herausforderungen und Überlegungen mit sich bringt. Es ist entscheidend, den Beizprozess von einer Fachkraft ausführen zu lassen.
Im folgenden Teil wird eine besondere Art des Beizens, das elektrolytische Beizen beschrieben.
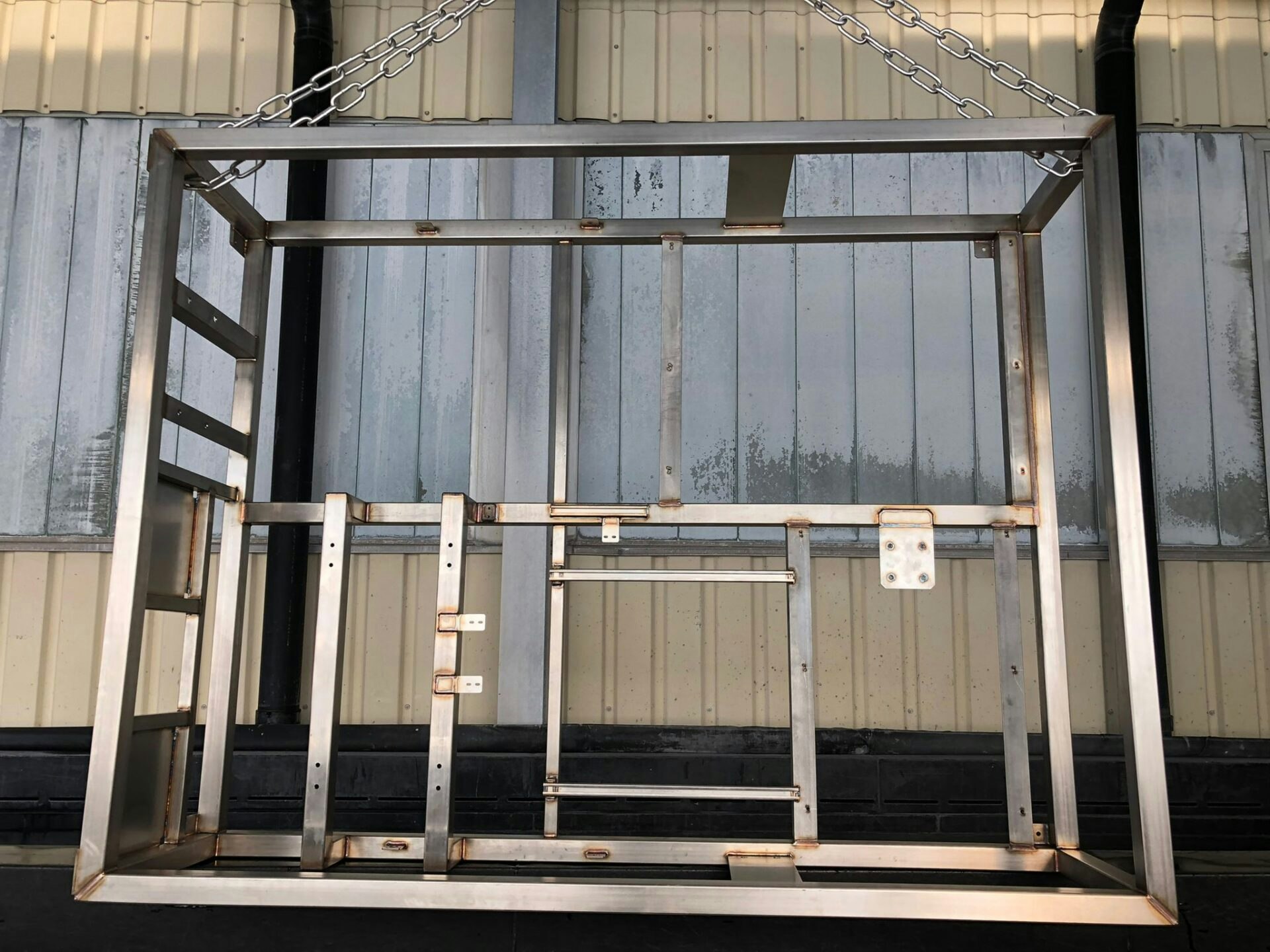
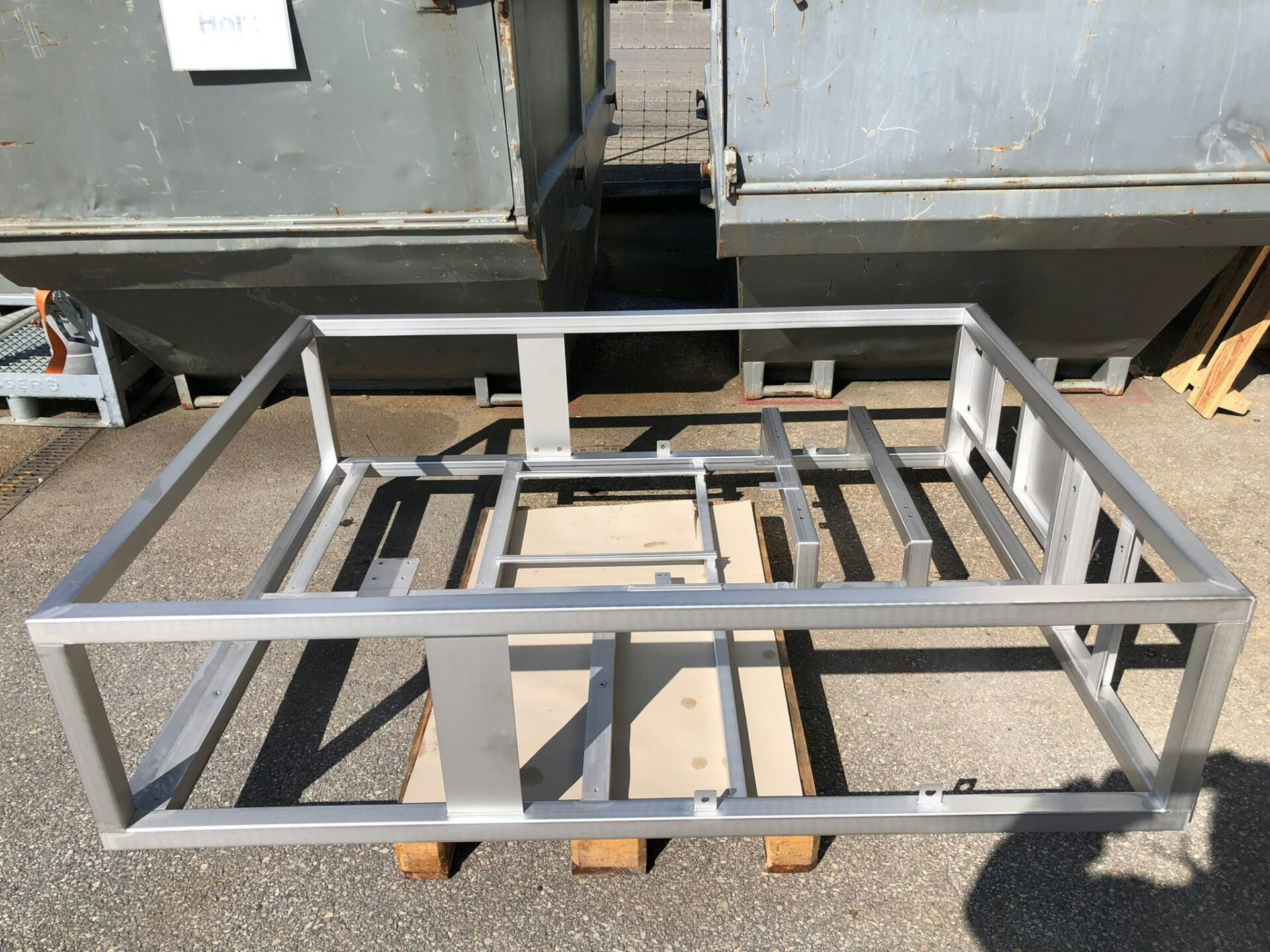
Elektrolytisches Beizen
Der Prozess des elektrolytischen Beizens, auch als elektrochemisches Beizen bekannt, ist eine weitere Methode zur Oberflächenbehandlung.
Der Prozess des elektrolytischen Beizens umfasst folgende Schritte:
Vorbereitung des Werkstücks: Das Werkstück wird zunächst gründlich gereinigt, um Schmutz, Öl und Fett zu entfernen. Dies ist wichtig, da diese Verunreinigungen die Effektivität des Beizprozesses beeinträchtigen könnten.
Aufbau des elektrolytischen Bades: Ein elektrolytisches Bad wird vorbereitet, das eine spezielle Beizlösung enthält. Diese Lösung besteht normalerweise aus einer Mischung von Säuren, Salzen und anderen Zusätzen, die für den Beizprozess notwendig sind. Die genaue Zusammensetzung hängt von den Eigenschaften des Werkstücks und dem gewünschten Ergebnis ab.
Einrichtung des elektrolytischen Beizbads: Das zu bearbeitende Stück wird als Anode (positiv geladenes Elektrode) in das elektrolytische Beizbad eingetaucht. Eine Gegenelektrode, üblicherweise aus Edelstahl, fungiert als Kathode (negativ geladene Elektrode). Beide Elektroden sind mit einer Stromquelle verbunden.
Anlegen von Strom: Ein Gleichstrom wird durch die Elektroden geleitet. Dies erzeugt eine elektrochemische Reaktion an der Oberfläche des Werkstücks. Oxidationsschichten und Verunreinigungen werden dabei gelöst und in der Beizlösung aufgelöst.
Elektrochemische Reaktionen: Während des elektrolytischen Beizens finden an der Werkstückoberfläche verschiedene elektrochemische Reaktionen statt. An der Anode (Werkstückoberfläche) werden Metallionen gelöst, während an der Kathode (Gegenelektrode) Wasserstoffgas erzeugt wird.
Entfernen der Oxidationsschichten: Die elektrochemischen Reaktionen führen dazu, dass Oxidationsschichten und Verunreinigungen von der Werkstückoberfläche abgetragen werden. Dies führt zu einer glatteren und saubereren Oberfläche.
Kontrolle des Prozesses: Der Beizprozess wird sorgfältig überwacht, um sicherzustellen, dass das gewünschte Ergebnis erzielt wird. Die Stromstärke, die Beizdauer und die Zusammensetzung des elektrolytischen Bades können je nach Werkstück und Ziel unterschiedlich eingestellt werden.
Spülung und Neutralisation: Nach dem elektrolytischen Beizen wird das Werkstück gründlich mit Wasser gespült, um die restlichen Beizrückstände zu entfernen. Dies wird oft von einer Neutralisation begleitet, um sicherzustellen, dass eventuell verbleibende Säurereste neutralisiert werden.
Trocknung und Abschluss: Das gereinigte und gebeizte Werkstück wird getrocknet und kann je nach Anwendungsbereich weitere Schritte wie Passivierung oder Beschichtung durchlaufen.
Der elektrolytische Beizprozess bietet den Vorteil, dass er zu keiner übermassigen Oberflächenrauheit führt, was beim normalen chemischen Beizen durchaus der Fall sein kann. Der Prozess ist präzise kontrollierbar und eine gleichmässige Oberflächenbehandlung wird ermöglicht.
Ein weiterer wichtiger Prozess der Oberflächenbehandlung ist die Passivierung. Im folgenden Teil wird dieser Prozess dargestellt und ein Einblick gegeben, was die Passivierung für eine Auswirkung auf den Edelstahl hat.
Passivierung
Für Werkstücke, die unmittelbar nach dem Beizen oder Elektropolieren chemisch beansprucht werden, ist eine Passivierung des Edelstahls zu empfehlen. Durch das Passivieren von Edelstahl wird der natürliche Vorgang der Passivschichtbildung chemisch beschleunigt und die Korrosionsbeständigkeit des Werkstoffs merklich verbessert. Dabei werden die Produkte in ein Passivierungsbad eingetaucht.
Ein Passivierungsbad enthält in der Regel eine Säurelösung, die speziell auf die zu behandelnden Metalle abgestimmt ist. Typischerweise werden rostfreie Stähle, insbesondere austenitische rostfreie Stähle wie 304 (1.4301) oder 316 (1.4401), passiviert. Der Prozess kann nach dem Beizen oder nach anderen Oberflächenbehandlungen durchgeführt werden, um die Bildung einer schützenden Passivschicht zu fördern.
Die Passivierung erfolgt in einer Lösung aus reiner 18- bis 25-prozentiger Salpetersäure (HNO3). Die Temperatur beträgt normalerweise 20 bis 50 Grad und der Prozess dauert höchstens eine Stunde. Das Passivierungsbad sollte ausserdem immer mit demineralisiertem Wasser statt mit Leitungswasser verdünnt werden. Das Passivierungsbad ähnelt einer Beize, aber die Wirkungsweise ist anders. Es ist ein wesentlich milderer Prozess aufgrund des Fehlens eines Aktivators.
Entsprechend kann kein Oxidfilm oder Chromoxide entfernt werden, jedoch können alle Sorten nichtrostenden Stahls passiviert werden.
Es ist wichtig zu wissen, dass eine Passivierung die natürliche Schicht des Stahls aus Chromoxiden und somit auch den Oxidfilm oder die entchromte Schicht des Stahls nicht aufzulösen vermag.
Eine weitere Massnahme um Edelstahl von Verunreinigungen zu befreien, ist die Dekontaminierung. Im folgenden Teil wird auf diesen Prozess eingegangen.
Dekontaminierung
In Bezug auf Edelstahl können Dekontaminierungsbäder verwendet werden, um hartnäckige Verschmutzungen oder Verunreinigungen von Edelstahloberflächen zu entfernen. Die Flüssigkeiten oder Lösungen in diesen Bädern bestehen normalerweise aus einer 2- bis 10-prozentigen Säure wie beispielsweise Phosphorsäure, Ameisensäure o.ä. Alle diese Säuren sind unschädlich für den nichtrostenden Stahl. Verunreinigungen sollen dadurch verschwinden und der Edelstahl soll so bleiben, wie er ist. Die Dekontaminierung ist im Vergleich zum Beizen viel einfacher durchzuführen. Auf Schutzausrüstung kann verzichtet werden und die Entsorgung des Abwassers ist weniger problematisch. Zusätzlich wirkt sich eine Dekontaminierung nicht negativ auf die Oberflächenrauheit aus.
Ein weiterer Prozess, welcher die Bearbeitung von Edelstahl ermöglicht, ist das Elektropolieren. Das Elektropolieren ist neben dem elektrolytischen Beizen der einzige Oberflächenprozess, der eine externe Stromquelle benötigt. Im folgenden Teil wird dieser Prozess dargestellt.
Elektropolieren
Das Elektropolieren ist ein elektrochemischer Prozess, der dazu dient, die Oberfläche von Edelstahl und anderen Metallen zu glätten, zu reinigen und zu veredeln. Dieser Prozess findet Anwendung in verschiedenen Branchen, darunter die Medizintechnik, die Pharmazie, die Lebensmittelverarbeitung, die Halbleiterindustrie und viele andere, wo höchste Reinheit, Korrosionsbeständigkeit und Ästhetik gefragt sind. Elektropolieren ist der einzige Prozess, mit dem die Korrosionsbeständigkeit im Vergleich zu einer normalen 2B-Oberläche wesentlich erhöht werden kann.
Die zu bearbeitenden Edelstahlteile werden als Anoden (positiv geladene Elektroden) in den Elektrolyten eingetaucht. Ein Elektrolyt enthält spezifische Chemikalien, die eine elektropolierende Wirkung auf das Metall haben. Eine Gleichstromquelle wird angeschlossen, wobei die Edelstahlteile als Anode und ein anderes Metallstück oder eine Platinelektrode als Kathode (negativ geladene Elektrode) fungieren. Ein stetiger elektrischer Strom fliesst zwischen den Elektroden. Während des Elektropolierens lösen sich an der Oberfläche des Edelstahls Metallionen ab. An der Anode findet eine entsprechende Oxidation statt. Dieser Prozess wirkt selektiv auf die Erhebungen und Unregelmässigkeiten der Oberfläche, wodurch sie geglättet werden. Während des Prozesses werden Unregelmässigkeiten, Mikrostrukturen und Verunreinigungen von der Edelstahloberfläche entfernt. Dies führt zu einer glatten, reflektierenden Oberfläche, die frei von Kratzern, Rissen und anderen Defekten ist.
Elektropolieren bewirkt auch eine verstärkte Passivierung des Edelstahls. Dies bedeutet, dass sich eine dünne, dichte Chromoxidschicht auf der Oberfläche bildet, die die Korrosionsbeständigkeit erhöht. Wenn das Material aber nicht direkt nach dem Elektropolieren verwendet wird, reicht eine Luftpassivierung aus, um die schützende Oxidschicht und die damit zusammenhängende Korrosionsbeständigkeit wiederherzustellen.
Welche Stahlsorten lassen sich nicht elektropolieren?
Martensite aber auch die niedrigstlegierten Ferrite sind nicht für das Elektropolieren geeignet.
Schwefellegierter Automatenstahl (1.4305). Dies ist auf seine geringe Beständigkeit gegen die allgemeine Korrosion zurückzuführen.
Generell kann man festhalten, dass Ferrite im Vergleich zu den Austeniten betreffend einer Säurebehandlung weniger beständig sind und sich dadurch für das Elektropolieren weniger eignen.
Es muss berücksichtigt werden, dass titanstabilisierte Austenite, wie beispielsweise die Güten 1.4541 und 1.4571, für das Elektropolieren nicht geeignet sind.
Das Elektropolieren bringt eine Vielzahl an Vorteilen:
Produkte mit maximaler Korrosionsbeständigkeit
Extrem hohe Reinigungsfreundlichkeit im Vergleich mit mechanisch bearbeiteten Oberflächen
Geringes Risiko von Bakterienwachstum
Verringerung von Oberflächenspannung in gedrehten oder geschliffenen Komponenten
Vorteil einer Anwendung bei komplexen Werkstücken, bei denen das mechanische Polieren nicht möglich ist etc.
Die Nachteile des Elektropolieren sind u.a.:
Der Bedarf einer aufwendigen Ausrüstung
Die Säuren erfordern ein hohes Mass an Sicherheit
Elektropolieren ist teuer
Die Erzielung einer homogenen Fläche ist schwer zu erreichen
Die aufwendige Temperatureinhaltung und kontinuierliche Badkontrolle
Fazit
Die chemische und elektrochemische Oberflächenbehandlung von Edelstahl eröffnet glanzvolle Aussichten und verleiht diesem Material eine strahlende Präsenz.
Folgende chemische und elektrochemische Verfahren sind die gängigsten Methoden, um Oberflächen von Edelstahl zu bearbeiten:
Beizen
Elektrolytisches Beizen
Passivierung
Elektropolieren
Diese Verfahren ermöglichen es, die Oberfläche gezielt zu bearbeiten und gleichzeitig die Materialeigenschaften zu beeinflussen. Dadurch sind präzise Anpassungen und eine hohe Qualität der Produkte gewährleistet. Die Oberflächenbehandlung von Edelstahl hat zudem den Vorteil, dass sie vielseitig einsetzbar ist. Sie kann in verschiedenen Industriesektoren angewendet werden, von der Automobilindustrie bis zur Lebensmittelverarbeitung. Dadurch eröffnen sich zahlreiche Möglichkeiten für den Einsatz von Edelstahlkomponenten. Insgesamt lässt sich festhalten, dass die chemische Oberflächenbehandlung von Edelstahl eine reizvolle Option für die Verbesserung von Oberflächeneigenschaften ist. Mit diesem Verfahren werden Edelstahlkomponenten nicht nur vor Korrosion geschützt, sondern erhalten auch eine glänzende und hochwertige Optik. Die Vielseitigkeit und die technischen Vorteile machen die chemische Oberflächenbehandlung zu einer optimalen Wahl für die Weiterverarbeitung von Edelstahl.
Es ist entscheidend, dass die Bearbeitung von Fachkräften unter Einhaltung der Sicherheitsvorschriften umgesetzt wird. Nur eine richtige Anwendung der Verfahren führt zum gewünschten Resultat.
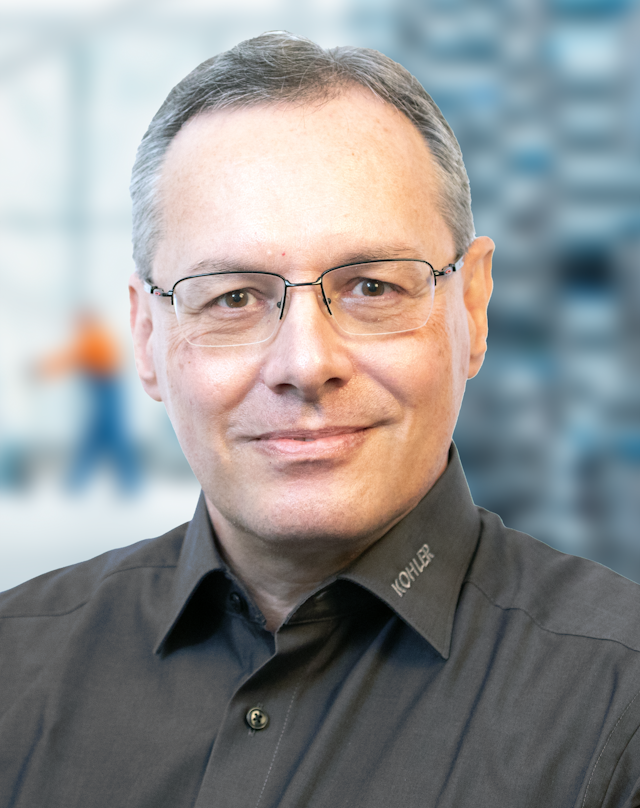
Haben Sie Fragen? Ich berate Sie gerne!
Kontakt
Dr. René Mächler
Leiter Qualitätsmanagement & Technik / Dipl. Werkstoffingenieur ETH
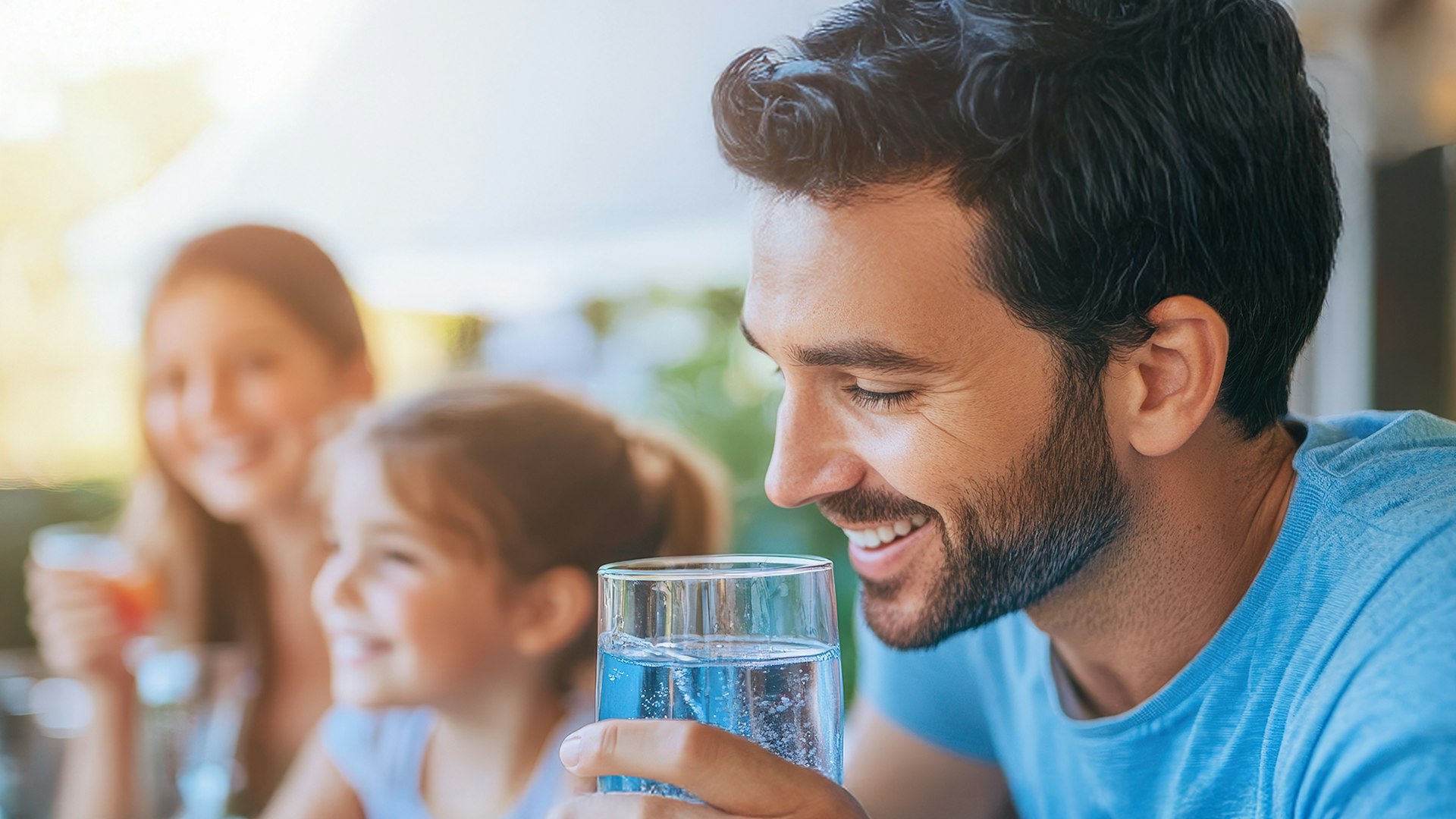
- Fachwissen
- Anwendungsbeispiel
- Referenzen
- Beratung
Alles über das Projekt «Erweiterung ARA Basel» zur Verbesserung der Abwasserreinigung
Die Abwasserreinigungsanlagen und Edelstahl sind eine unverzichtbare Kombination, um Trinkwasser in einer hohen Qualität der Bevölkerung bereitzustellen.

Sinnstiftende Partnerschaften: KOHLER fördert Sport, Innovation und Wissenschaft
KOHLER legt grossen Wert darauf, bedeutsame Aktivitäten zu fördern und sich in einem engagierten Netzwerk als aktive Playerin zu positionieren.
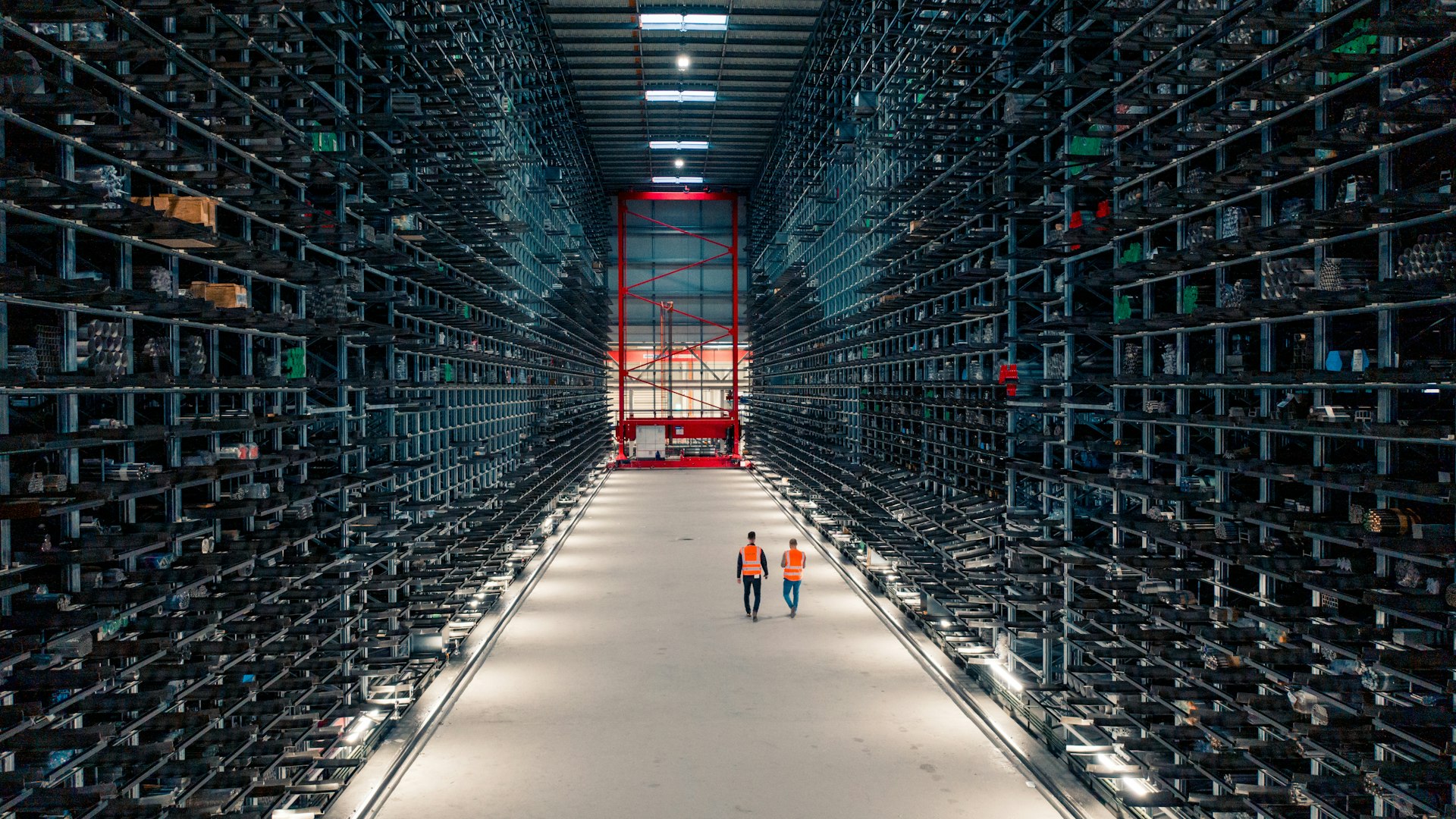
HANS KOHLER AG - Ihre Nr. 1 für Edelstahl
Die HANS KOHLER AG ist eine eigenständige, unabhängige Handelsunternehmung mit Sitz in Zürich.