Fallstudie «Papieri Areal», Hälg & Co. AG
Fallstudien
Auf dem «Papieri Areal» in Cham (Kanton Zug) entwickelt die Cham Group ein neues Wohn- und Arbeitsquartier mit industriellem Charme. Direkt an der Lorze werden prägende Bestandsbauten der ursprünglichen Papierfabrik mit markanten Neubauten ergänzt und nachhaltig realisiert. Die Hälg & Co. AG Luzern wurde für die Realisierung der Heizungs-, Kälte- und Sanitäranalgen beauftragt. In folgendem Interview nimmt Herr Pashk Bezhi als Projektleiter bei Hälg & Co. Stellung zur Realisierung dieses Projektes.

Marketingfachfrau
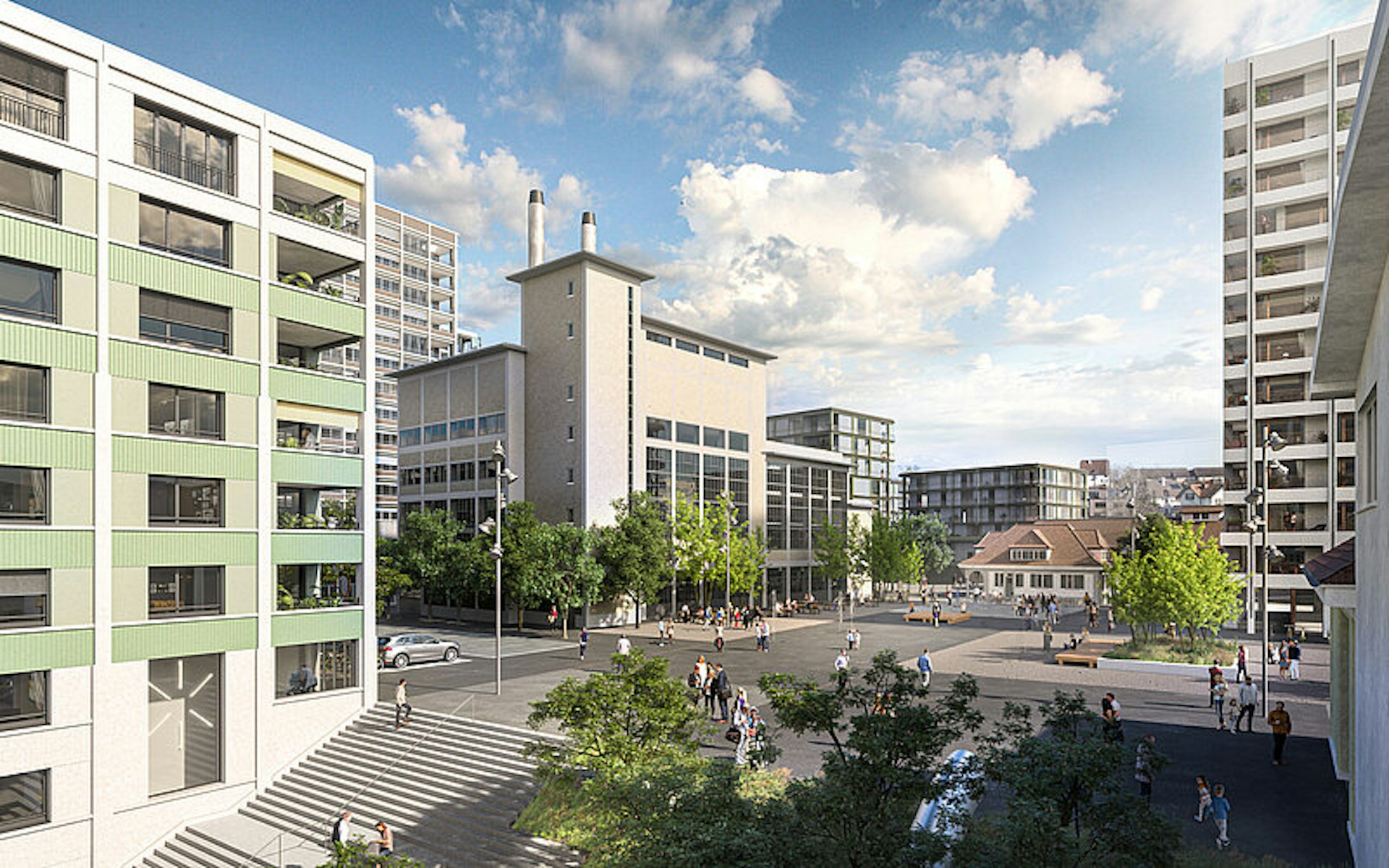
Guten Tag, Herr Bezhi. Vielen Dank, dass Sie sich die Zeit genommen haben, um mit uns über das Projekt «Papieri Areal» in Cham zu sprechen. Können Sie uns bitte einen Einblick in Ihre Arbeit und Rolle bei der Hälg & Co. AG geben?
Ich bin seit 13 Jahren bei der Firma Hälg tätig, angefangen 2010 als Haustechnikplaner im Bereich Heizung, danach war ich für die Projektleitung zuständig. In den letzten 5 Jahre habe ich vermehrt Grossprojekte geleitet und realisiert. Seit gut einem Jahr leite ich die Abteilung Heizung/Kälte mit 8 Mitarbeitenden am Standort Ebikon. Das Projekt «Papieri Areal Cham» konnte ich als Projektleiter begleiten und erfolgreich umsetzen.
Welche Rolle spielte die Hälg & Co. AG bei dem Neubau des «Papieri Areals»?
Die Firma Hälg & Co. AG führte bei diesem Projekt mehrere Aufträge aus. Die Realisierung der Energiezentrale, die Fernleitungen, also alle Leitungen, die sich im Boden befinden und sich über das ganze Areal erstrecken und damit die gesamte Versorgung der 15 Gebäude sicherstellen, wurden durch die Hälg & Co. AG durchgeführt.
Zusätzlich durften wir alle Wärme- und Kälteleitungen von den Gebäuden bis zu den jeweiligen Übergabestationen der einzelnen Gebäude installieren. Die Übergabestationen wurden ebenfalls von Hälg geliefert. In Summe sind dies 66 Stück, welche sich jeweils in einem Metallgerüst befinden und mit Wärmetauschern ausgestattet sind. Ausserdem durften wir den gesamten Auftrag mit Glykol befüllen. Hierfür wurde ein separater Auftrag erteilt. Das heisst, wir haben die Primärwärme- und Kälteleitungen bis zu den einzelnen Gebäuden installiert. Die gesamten Heizungs-, Kälte- und Sanitäranlagen wurden von uns realisiert. Das Projekt ist bereits zu ca. 65% abgeschlossen, nächstes Jahr folgen weitere Kälteanlagen, danach wird jedes weitere Gebäude, das in den nächsten Jahren gebaut wird, sukzessive an die Leitungen angeschlossen. Wir sind jetzt seit drei Jahren in der Bauphase, die gesamte Bauzeit beträgt ca. 15 Jahre.
Die Hälg & Co. AG wurde für die Wärmeerzeugung inkl. der sanitären Anlagen beauftragt. Wie werden solch grosse Projekte organisiert?
Die grösste Herausforderung stellt die zeitliche Komponente dar, d.h., bis wann welches Volumen realisiert werden muss. Beispielsweise die Energiezentrale mit einem Auftragswert von 2 Mio. CHF, musste innerhalb von 6 Monaten installiert werden. Die Organisation ist bei jedem Grossprojekt das A und O. Wir haben versucht, dies mit den verfügbaren Ressourcen umzusetzen, um am Tag X die Wärme und Kälte erfolgreich zu übergeben und bereitzustellen.
Nach Erhalt des Auftrags wird an der Kick-off-Sitzung die grundlegende Organisationsstruktur festgelegt. Es wird geklärt, welche Herausforderungen in welchem Zeitrahmen gemeistert werden müssen. Die Lieferzeiten der Kälteanlagen sind besonders knifflig, weil sie lange brauchen, bis sie ankommen. Deshalb ist es wichtig, rechtzeitig die Bestellungen aufzugeben, damit man nicht zeitlich unter Druck gerät. Eine vorausschauende Planung ist enorm wichtig. Wir haben an diesem Projekt inmitten der Corona-Pandemie gearbeitet, die Lieferprobleme wurden zu einem merklichen Hindernis. Hier mussten wir Lösungen finden, um die Fristen trotzdem zu erfüllen.
Was waren die wichtigsten Erkenntnisse oder Erfolge, die während des Projekts erzielt wurden, insbesondere in Bezug auf die Qualität der ausgeführten Arbeiten?
Das Hauptziel eines Projekts besteht darin, die Fertigstellung termingerecht zu erreichen. In diesem Projekt hatten wir mehrere Teilaufträge. Für mich war insbesondere der Abschluss der Erdleitungen ein besonders bedeutender Abschnitt. Nachdem der Graben ausgehoben, die vier bis acht Leitungen geschweisst, eingebaut und der Graben wieder geschlossen und asphaltiert wurde, konnte dieser Abschnitt der Erdleitung als abgeschlossen betrachtet werden. Dieser Schritt war und ist immer einen bedeutenden Meilenstein in einem solchen Grossprojekt. Der Abschluss dieser Etappe war für mich ein zentraler Erfolgsbaustein für die Realisierung des Gesamtprojektes.
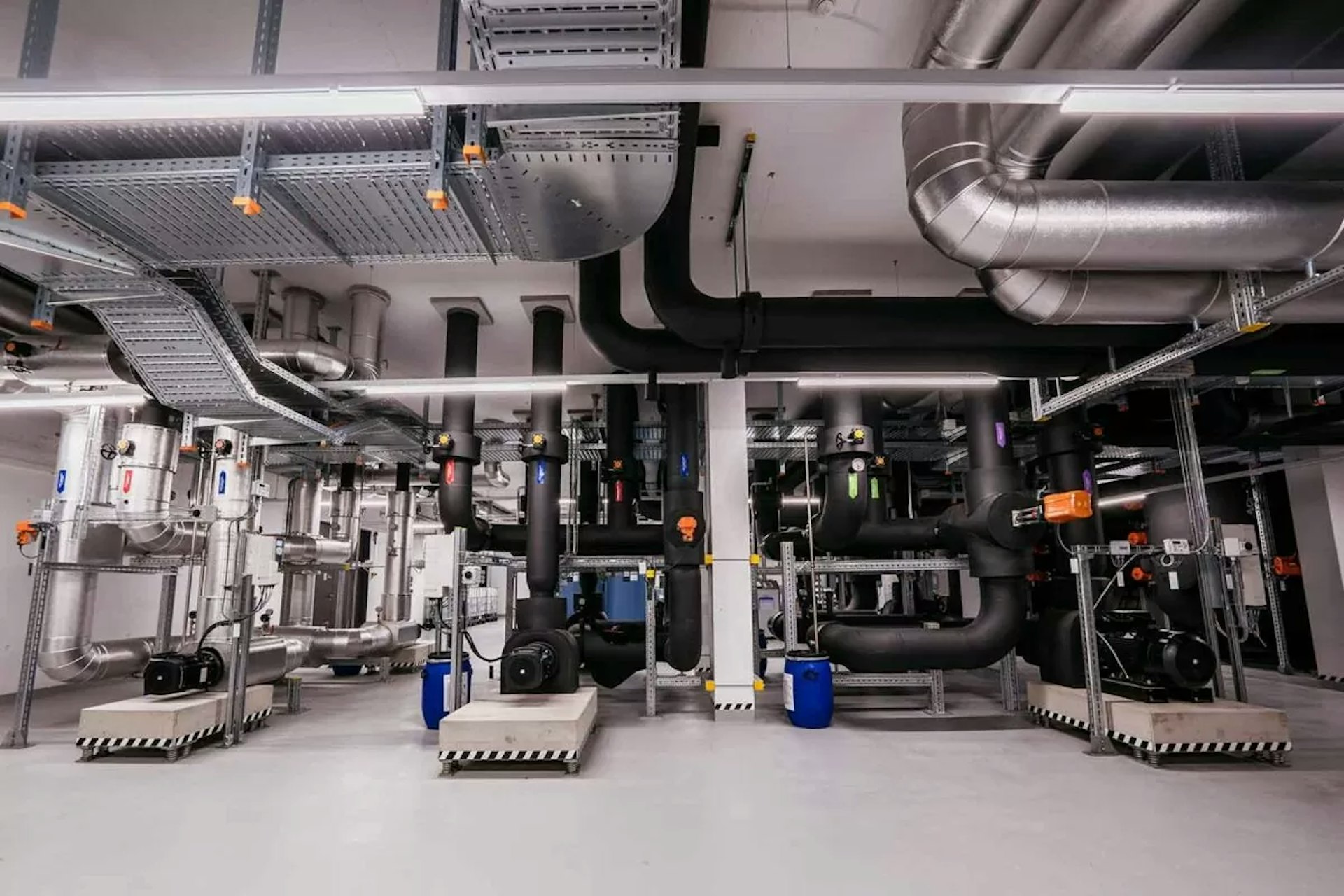
Gibt es besondere Herausforderungen beim Bau dieser Erdleitungen?
Eine besondere Herausforderung stellt ohne Zweifel das Wetter dar. Da die Erdleitungen innerhalb eines Jahres realisiert wurden, haben wir alle vier Jahreszeiten durchlebt. Im Sommer beispielsweise, erhitzten sich die Rohre und die Sonne strahlte direkt in den Graben, während man Schweissarbeiten durchführt. Im Winter waren die Rohre kalt und teilweise eingefroren. Bei Regen füllte sich der Graben mit Wasser, welches abgepumpt werden musste. Nur so waren Schweissarbeiten an den Leitungen überhaupt möglich. Teilweise mussten Zelte aufgestellt werden, damit bei Durchzug röntgensicher geschweisst werden konnte. Eine weitere Herausforderung bestand im Transport der 12 Meter langen Fernleitungsrohre.
Welche drei Punkte sind für Sie bei der Umsetzung von solchen Grossprojekten von grosser Bedeutung?
Wir sind auf Just-in-time-Lieferungen angewiesen. Daher bevorzugen wir Lieferanten, die das von uns benötigte Material vorrätig haben, da wir selbst kein Material lagern. Unsere Bestellungen sind immer projektbezogen.
Ausserdem setzen wir auf eine gute Kommunikation mit den Spediteuren. Sobald es sich um grosse Projekte handelt, vertrauen wir auf eine pünktliche Lieferung. Das bedeutet, dass die Lieferung in genauen Zeitfenstern erfolgen müssen, da anschliessend das Material verwendet wird und die Mitarbeitenden nur einen kurzen Zeitraum für Entgegennahme der Materialien zur Verfügung haben. Besonders problematisch wird es, wenn Spediteure das Material ohne vorherige telefonische Benachrichtigung auf der Baustelle abliefern und deponieren. Oft befinden sich die Monteure in einem Keller ohne Empfang. Hier ist es wichtig, dass Spediteure Geduld zeigen. Wenn sie nicht bereit sind, 10 Minuten zu warten, kann dies dazu führen, dass wir den Rest des Tages damit verbringen, das Material auf der Baustelle zu suchen um es dann von A nach B zu transportieren. Das verursacht erhebliche Zeitverluste. Wenn zum Beispiel ein Teil des Geländes zu einer bestimmten Zeit betoniert wird, ist es unmöglich, mit den Lastwagen dorthin zu fahren. Deshalb ist es sehr wichtig, die Zeiträume für Anlieferungen strikte einzuhalten.
Teamwork auf der Baustelle, mit den Lieferanten und auch intern ist das A und O. Ausserdem ist jeder auf jeden angewiesen, d.h. Zuverlässigkeit ist ein wichtiges Erfolgskriterium. Auf den Baustellen ist es sehr hektisch, die verfügbare Zeit ist auf ein Minimum beschränkt. Wir machen auch die Erfahrung, dass in der Planung und in der Entscheidungsfindung bei Projekten sehr viel Zeit in Anspruch genommen wird, welche dann bei den Ausführungsarbeiten teilweise fehlt.
Wie wichtig sind Lieferanten für euch in diesen grossen Projekten?
Sehr wichtig, vor allem in Bezug auf termingerechte Lieferungen. Wenn wir wissen, dass es sich beim Auftrag beispielsweise um sehr grosse, sehr dickwandige oder auch nahtlose Rohre handelt, haben wir die Erfahrung gemacht, dass eine frühzeitige Bestellung von grosser Bedeutung ist. Hierfür brauchen wir Lieferanten, wie die HANS KOHLER AG, die spezifische Produkte in möglichst kurzer Zeit organisieren und Standardprodukte direkt ab Lager liefern können.
Welche Edelstahlqualitäten wurden eingesetzt und warum?
Hauptsächlich wurden Werkstoffe 1.4301 und 1.4404 angewendet. In der Energiezentrale haben wir sogar für den ganzen Heiz- und Kühlbereich Chromstahl verwendet. Normalerweise genügt Schwarzstahl für den Heizbereich, während Chromstahl für den Kühlbereich eingesetzt wird. Aufgrund unserer Spezialisierung in der Verarbeitung von Chromstahl haben wir die Möglichkeit komplette Anlagen inkl. der Heizung in Chromstahl zu offerieren und im Vergleich zu anderen Materialien auf gleichem Kostenniveau anzubieten. Dies wurde auch beim «Papieri Areal» umgesetzt.
Welche Vorteile bot das gewählte Material für die Umsetzung der Wärme- und Kälteversorgung? Insbesondere auch auf den oben genannten Punkt, die Heizung in Chromstahl auszuführen?
Die Hälg & Co. AG in Luzern ist besonders erfahren in der Verarbeitung von Chromstahl, welcher im Vergleich zu anderen Materialien einfacher zu bearbeiten ist. Beispielsweise ermöglichen die dünneren Wandstärken von Chromstahl eine leichtere Handhabung und eine Reduzierung des Gesamtgewichts, was weniger Manpower und Hebezeug auf der Baustelle erfordert. Da für jedes Hebemittel Miete bezahlt werden muss, ergibt sich insgesamt eine Kostenneutralität. Entsprechend haben wir uns entschieden auch die Heizung in Chromstahl anstelle von Stahl anzubieten. Darüber hinaus bietet Chromstahl den Vorteil, dass er nicht rostet, insbesondere in Umgebungen, in denen Kälte und Kondenswasser vorhanden sind.
Können Sie auf die Herausforderungen eingehen, die beim Neubau des «Papieri Areals» in Cham auftraten, insbesondere in Bezug auf die Dimensionen der Leitungen und der Logistik des Materials?
Auf der Baustelle traten aufgrund der grossen Dimensionen erhebliche Lagerprobleme auf. Wir hatten zwar einen Aussenbereich für die Materiallagerung, aber aufgrund der eingeschränkten Platzverhältnisse mussten wir das Material ständig verschieben. Besonders bei grossen Rohren mit einem Durchmesser von DN300 war das nicht einfach und zeitintensiv.
Eine weitere Herausforderung bestand darin, Abfälle wie Restmaterial oder Paletten zu entsorgen. Grosse Rohre werden in Holzkisten geliefert oder Fittings auf Paletten. Bei grossen Dimensionen entstand das Problem, dass wir hinterher eine beträchtliche Menge entsorgen mussten.
Eine präzise Kennzeichnung des Materials ist ebenso entscheidend. Es ist von grosser Bedeutung, dass wir klar nachvollziehen können, welches Material an welchen Ort gehört. Fehlt die Beschriftung des Materials, gestaltet sich die Zuordnung vor Ort für den Arbeiter immer schwierig.
Wie wurden die angesprochenen Probleme während des Prozesses bewältigt?
Es ist entscheidend, Missverständnisse zwischen dem Lieferanten und uns auszuräumen und miteinander klar und direkt zu kommunizieren. Nur so können solche Grossprojekte erfolgreich realisiert werden. Hier möchte ich betonen, dass das KOHLER-Haustechnikteam äusserst lösungsorientiert war. Die Bereitschaft und das Engagement haben wir sehr geschätzt, innerhalb kurzer Zeit wurde ein Lösungsvorschlag vom Team der HANS KOHLER AG erarbeitet, um das Thema der beschränkten Platzverhältnisse zu meistern. Selbst während der Corona-Pandemie, als wir mit Lieferschwierigkeiten konfrontiert waren, wurden uns Lösungen angeboten, wie Direktlieferungen aus Schweden oder Italien. Wir spüren, dass wir von der HANS KOHLER AG massgeschneiderte Lösungen erhalten, die auf unsere Bedürfnisse zugeschnitten sind.
Gab es während des Projekts Herausforderungen oder Schwierigkeiten im Zusammenhang mit dem gewählten Material?
Ja, das war tatsächlich so. Probleme traten im Zusammenhang mit den Wandstärken der ANSI-Rohre auf. Die Schwierigkeit besteht darin, dass der ANSI-Toleranzbereich sehr gross ist, was den Umgang damit manchmal erschwert. Bei röntgensicheren Schweissarbeiten haben wir beispielsweise ein ANSI-T-Stück mit einer Stärke von 10 mm und ein Rohr mit einer Stärke von 3 mm. Das bedeutet, dass wir die Wandstärke des T-Stücks auf 3 mm abschleifen müssen, um eine gleichmässige Dicke von konstant 3 mm zu erreichen. Bisher haben wir noch keine Maschinen oder Werkzeuge gefunden, die dies für uns erledigen könnten. Das lange Schleifen auf das gewünschte Mass stellt eine Herausforderung dar.
Wie hat die Erfahrung dieses Projekts die zukünftige Materialauswahl für ähnliche Projekte beeinflusst?
Wir haben aufgrund des röntgensicheren Schweissens zahlreiche Orbitalflansche verwendet. Unsere Anlagen werden vor der Inbetriebnahme geröntgt, um unsere hohen Standards sicherzustellen. Es ist daher nicht sinnvoll, normale Flansche zu verwenden. Stattdessen nutzen wir die gelieferten Orbitalflansche der HANS KOHLER AG, da sie in der passenden Wandstärke erhältlich sind. Es freut uns, dass ihr diese in eurem Sortiment führt.
Auch mit den Nenndrücken haben wir positive Erfahrungen gesammelt und viel daraus gelernt. Wir haben heute ein bedeutend besseres Verständnis, was die Druckbereiche der Rohre betrifft.
Es ist erfreulich, dass wir die Heizung ebenfalls aus Chromstahl gefertigt haben. Diesen Ansatz werden wir zukünftig verstärkt verfolgen und umsetzen. Wir sind optimistisch, dass dies vermehrt Anwendung finden wird. Ein weiterer Vorteil besteht darin, dass es bei einer reinen Anwendung von Chromstahl keine Materialvermischung gibt, was das Risiko von Verwechslungen minimiert. Dadurch kann auch Flugrost vermieden werden, da eine hundertprozentige Materialtrennung gewährleistet ist. Insbesondere bei den Pressfittings ist genaues Hinsehen erforderlich, um verzinkten Stahl nicht mit Chromstahl zu verwechseln.
Kann man sagen das dies ein eher neuer Trend ist, Orbitalflansche einzusetzen im Vergleich zu früher?
Ich würde nicht behaupten, dass dies ein neuer Trend ist. Es ist jedoch zu beobachten, dass wir eher bereit sind, etwas mehr für den Flansch zu bezahlen, um anschliessend den Bearbeitungsaufwand zu minimieren. Das ist im Rahmen eines solchen Projektes von grosser Bedeutung.
Hat dieses Projekt dazu geführt, dass Sie in Zukunft vermehrt mit der HANS KOHLER AG zusammenarbeiten?
Die HANS KOHLER AG ist ein sehr starker Partner für uns. Unsere fortlaufende Zusammenarbeit mit euch beruht nicht nur auf diesem Projekt, sondern auf einer Historie von erfolgreichen Projekten und einer ausgezeichneten Kooperation über viele Jahre hinweg. Unsere langjährige Partnerschaft mit KOHLER basiert auf sehr positiven Erfahrungen.
Wie schätzen Sie zukünftige Verwendungen von korrosionsbeständigem Stahl in Ihrem Unternehmen und in der Branche im Allgemeinen ein? Welche Entwicklungen erwarten Sie hinsichtlich der Materialauswahl und Anwendungsbereich?
In unserem Bereich sehe ich im Moment keine grossen Veränderungen oder Entwicklungen. Durch die Nutzung von Chromstahl im Bau von Heizungsanlagen, haben wir eine gute und kostenneutrale Alternative zu Schwarzstahl, welche wir gezielt nutzen und welche Vorteile mit sich bringt. Das bedeutet jedoch nicht zwangsläufig, dass es auch von anderen durchgeführt wird. Ich denke, dass Kunden bereit sind für Produkte mehr zu bezahlen, wenn der Service des Lieferanten, die Qualität der Produkte gegeben ist und der Bearbeitungsaufwand reduziert werden kann.
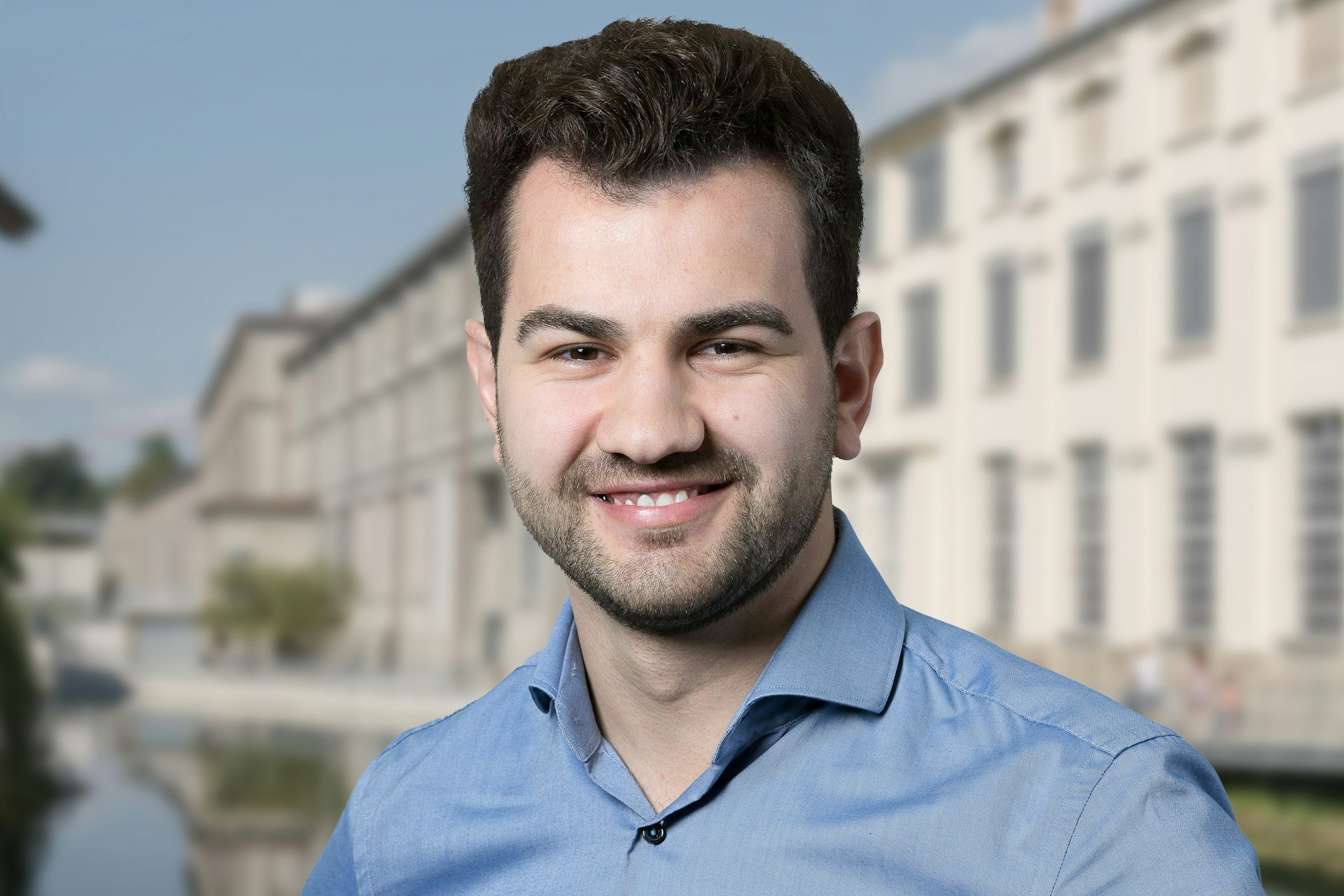
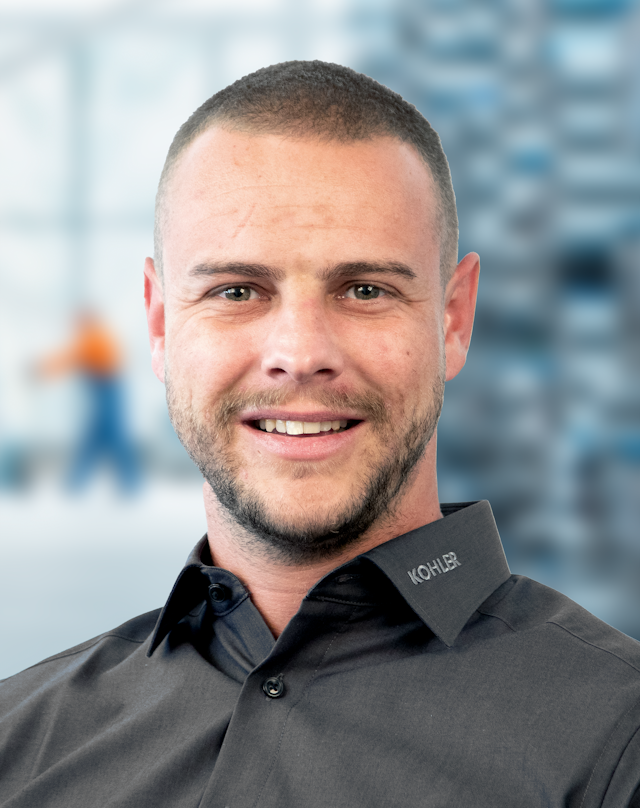
Haben Sie Fragen? Ich berate Sie gerne!
Kontakt
Ihr Wunschprodukt ist online nicht erhältlich oder Sie hätten gerne andere Masse? Rufen Sie uns an, gerne beantworten wir Ihre Fragen oder nehmen Ihre Bestellung telefonisch entgegen.
Marco Marti
Teamleiter «Haustechnik»
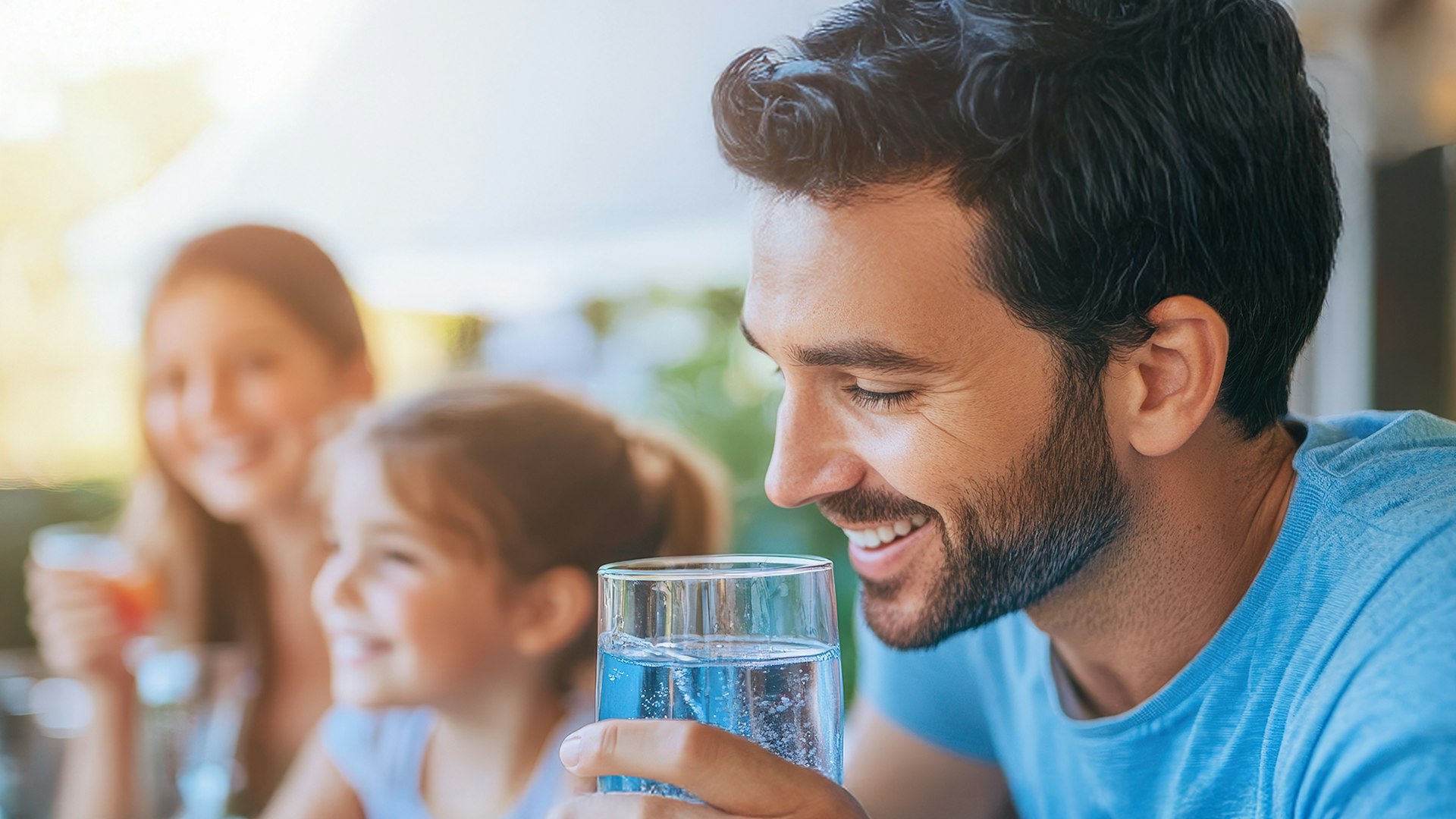
- Fachwissen
- Anwendungsbeispiel
- Referenzen
- Beratung
Alles über das Projekt «Erweiterung ARA Basel» zur Verbesserung der Abwasserreinigung
Die Abwasserreinigungsanlagen und Edelstahl sind eine unverzichtbare Kombination, um Trinkwasser in einer hohen Qualität der Bevölkerung bereitzustellen.

Sinnstiftende Partnerschaften: KOHLER fördert Sport, Innovation und Wissenschaft
KOHLER legt grossen Wert darauf, bedeutsame Aktivitäten zu fördern und sich in einem engagierten Netzwerk als aktive Playerin zu positionieren.
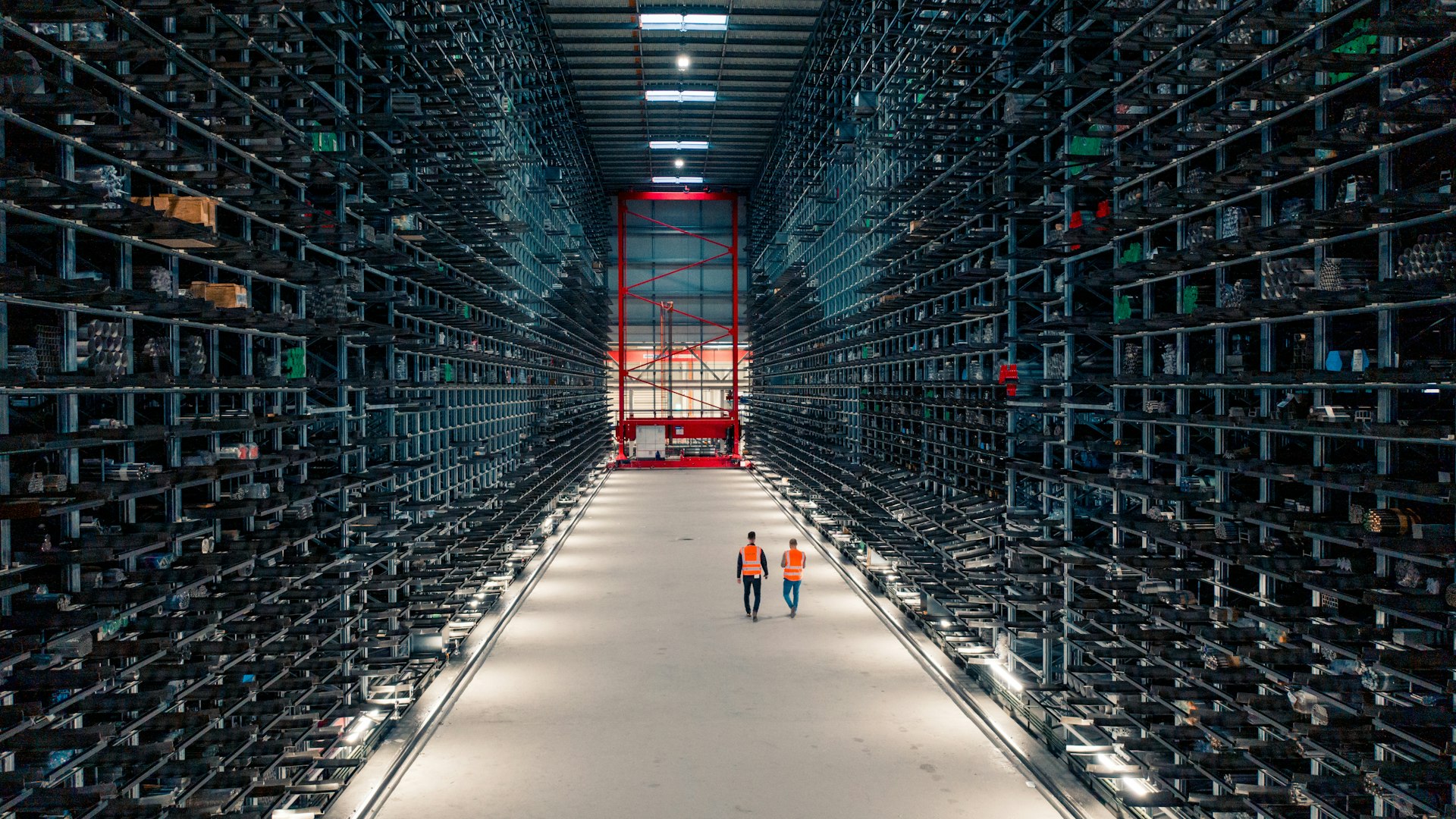
HANS KOHLER AG - Ihre Nr. 1 für Edelstahl
Die HANS KOHLER AG ist eine eigenständige, unabhängige Handelsunternehmung mit Sitz in Zürich.