Vom Erz zum Rohstahl: Eine faszinierende Reise durch die Welt der Metallurgie
Werkstoff Fachwissen
Vor langer Zeit setzte sich eine Gruppe von Jägern und Sammlern in den Bergen fest. Eines Tages stiessen sie auf ein seltsames Gestein, das schwer war und im Sonnenlicht glänzte. Sie nahmen es mit ins Lager und erkannten bald seinen Wert. Das Erz wurde abgebaut und bearbeitet, sodass Werkzeuge, Waffen sowie Kunstwerke entstanden. Das wertvolle Metall ist heute aus unserer Gesellschaft nicht wegzudenken.

Marketingfachfrau
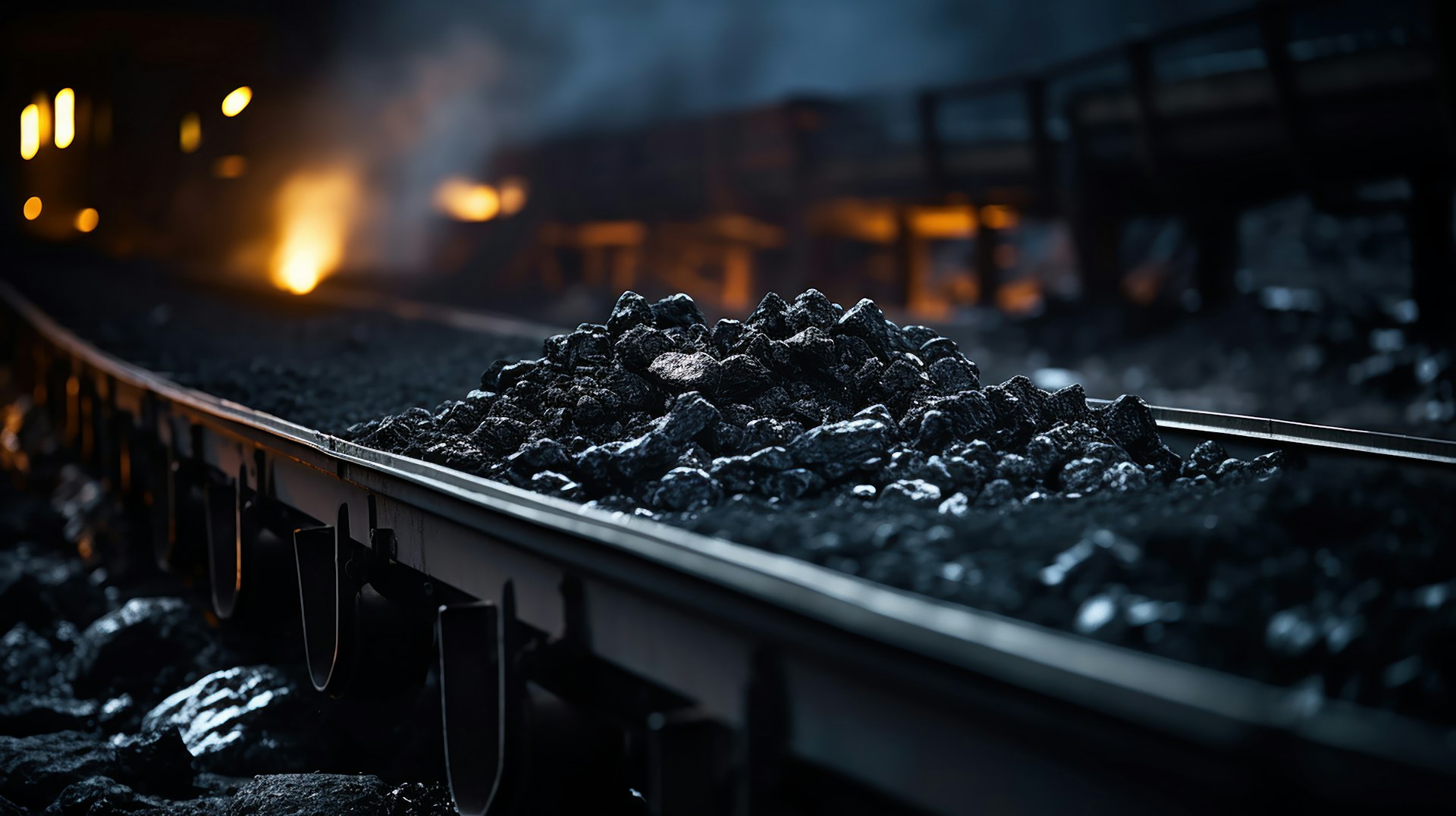
Erzgewinnung: Einblicke in Arten von Erzvorkommen
Die meisten Metalle, so auch Eisen, sind unedel. Sie kommen in der Natur nicht in reiner Form vor, sondern als chemische Verbindungen mit Sauerstoff, Schwefel und anderen Nichtmetallen. Lediglich Edelmetalle wie Gold findet man in gediegener Form.
Die Erzgewinnung ist der erste Schritt im langen Weg der Stahlherstellung. Um das wertvolle Erz zu gewinnen, müssen verschiedene Arten von Erzvorkommen identifiziert und abgebaut werden. Wichtige Eisenerzsorten sind:
Magnetit Fe3O4 (Magneteisenstein)
Hämatit Fe2O3 (Roteisenstein)
Limonit FeO(OH) (Brauneisenstein)
Siderit FeCO3 (Eisenspat)
Pyrit FeS2 (Eisenkies, “Katzengold”)
Jedes Erzvorkommen hat seine eigenen Eigenschaften und erfordert spezifische Bergbau- und Extraktionsmethoden.
Erzgewinnung im Bergbau
Beim Bergbau stehen verschiedene Techniken zur Verfügung, um Erz aus der Erde zu gewinnen.
Zu den gebräuchlichsten Verfahren gehören:

Der Tagebau
Tagebau ist ein Begriff innerhalb des Bergbaus. Er bezieht sich auf die Gewinnung von Bodenschätzen in oberflächennahen Bereichen. Zusätzlich zur technologischen Komponente wird die Einrichtung oder der Standort, an dem diese Technik angewendet wird, als Tagebergbau bezeichnet.
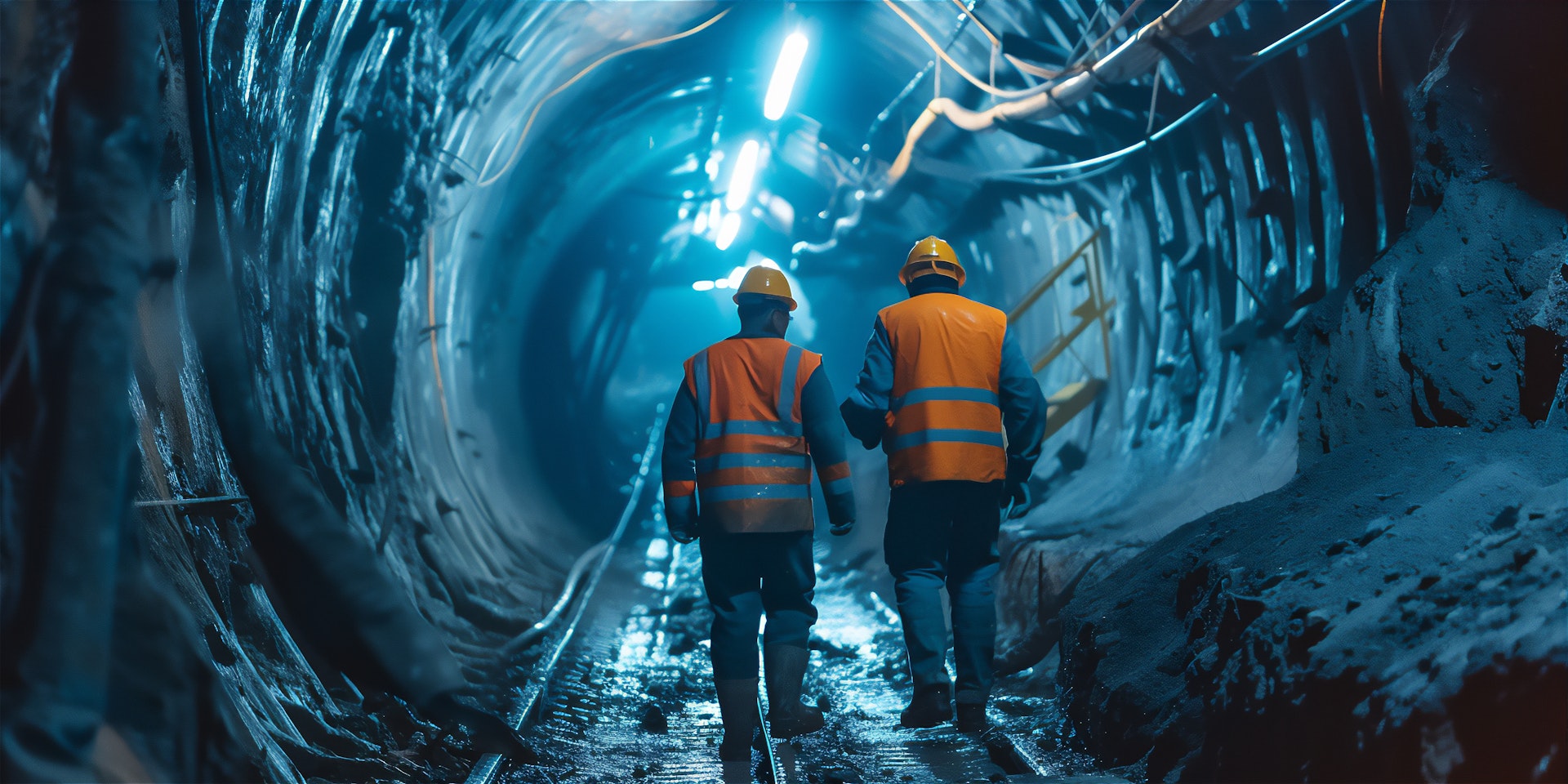
Der Untertagebau
Als Untertagebau bezeichnet man die Schaffung von Hohlräumen unter der Erdoberfläche, also im Gestein unter Tage. Im Zuge des Untertagebaus werden Bodenschätze erschlossen, die in tiefer gelegenen Lagerstätten vorhanden sind.
Die Bedeutung von Sinteranlagen in der Stahlproduktion
In der Welt der Stahlherstellung gibt es eine entscheidende Komponente, die oft im Schatten der glühenden Hochöfen und beeindruckenden Stahlwerke steht: die Sinteranlage. Doch diese scheinbar bescheidene Einrichtung spielt eine Schlüsselrolle in der Vorbehandlung von Eisenerzen und hat einen enormen Einfluss auf die Qualität und Effizienz der gesamten Stahlproduktion.
Eine Sinteranlage ist eine spezialisierte Einrichtung, die dazu dient, Eisenerze in ein poröses, festes Material «Sinter» umzuwandeln. Dieser Prozess des Agglomerierens oder Verfestigens der Erze ist von entscheidender Bedeutung, da er die Erze für den Einsatz in den Hochöfen eines Stahlwerks vorbereitet.
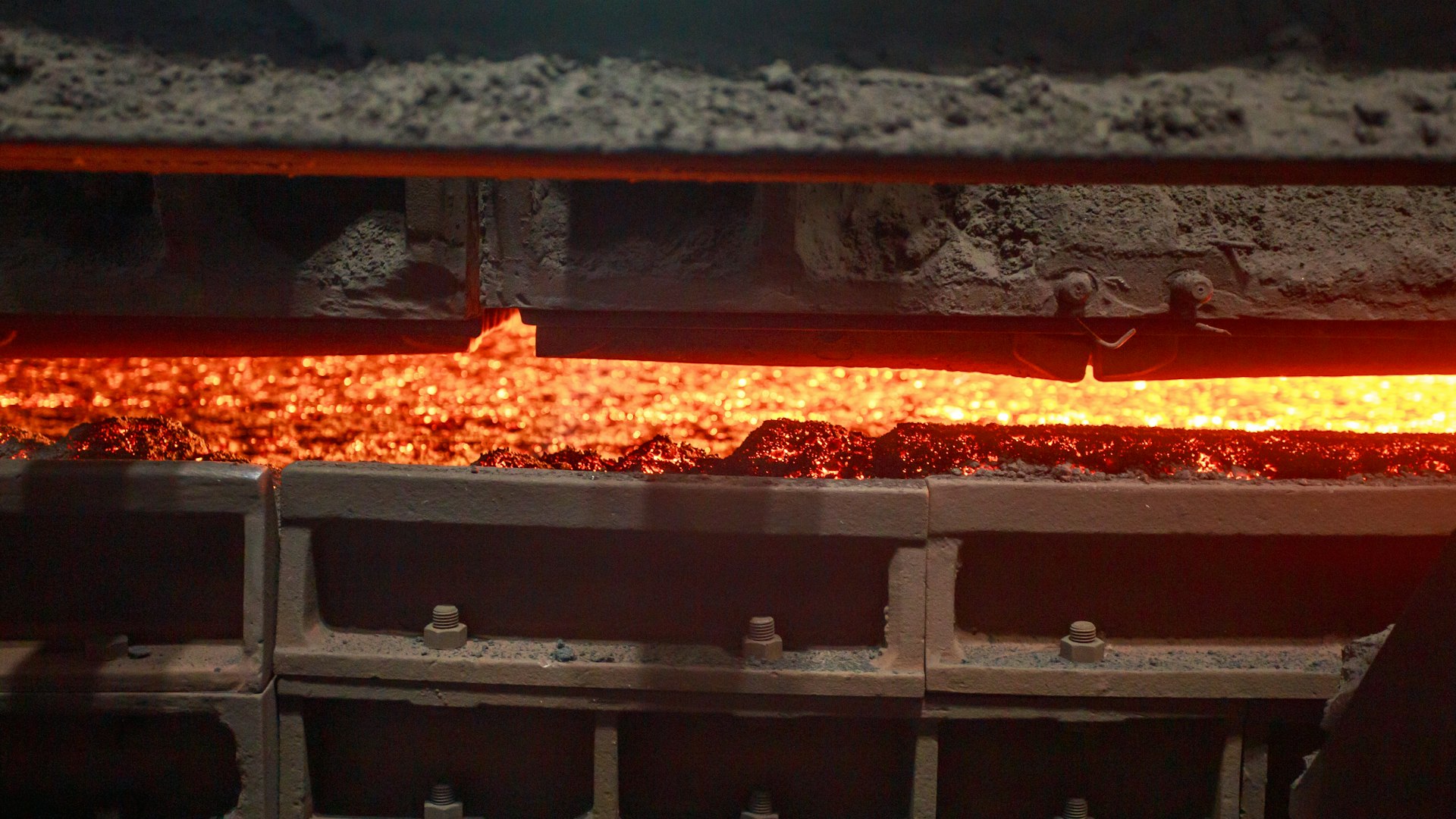
Was passiert beim Prozess:
Erzvorbehandlung: Eisenerze, die aus Minen gewonnen werden, sind selten in einer Form, die direkt in Hochöfen eingesetzt werden kann. Sie enthalten oft Verunreinigungen und sind zu feinkörnig, um effizient geschmolzen zu werden. Hier kommt die Sinteranlage ins Spiel. Sie erhitzt die Erze auf hohe Temperaturen und bringt sie zum Agglomerieren, wodurch sie in den für die Hochöfen geeigneten Sinter umgewandelt werden.
Verbesserung der Rohstoffqualität: Der Sinterprozess ermöglicht nicht nur die Entfernung gewisser Verunreinigungen, sondern auch die Mischung verschiedener Erzsorten. Dadurch kann die Homogenität und Qualität des Ausgangsmaterials erheblich verbessert werden.
Effizienzsteigerung: Sinter ist porös und ermöglicht eine gleichmässige Verteilung von Hitze und Reduktionsgasen in den Hochöfen. Dies führt zu einer effizienteren Verbrennung und Schmelze, was letztendlich den Energieverbrauch reduziert und die Produktivität erhöht.
Umweltauswirkungen: Durch den Einsatz von Sinteranlagen werden auch Umweltauswirkungen reduziert, da weniger Rohstoffe und Energie benötigt werden, um hochwertigen Stahl herzustellen. Dies trägt zur Nachhaltigkeit der Stahlproduktion bei.
Nachdem die Eisenerze den entscheidenden Agglomerationsprozess in der Sinteranlage durchlaufen haben, sind sie nun bereit für die nächste Phase ihrer Reise – die Reise ins Herz der Stahlherstellung, den Hochofen.
Der Hochofen und wie Roheisen entsteht
Fakten zum Hochofen
Hochöfen werden normalerweise für etwa 10 bis 15 Jahre ohne Unterbrechung betrieben. Nach dieser Zeit, die als «Ofenreise» bezeichnet wird, ist eine umfangreiche Überarbeitung des Hochofens erforderlich
Mittlere Hochöfen erreichen Tagesleistungen von 6000 Tonnen, grosse Hochöfen bis zu 13 000 Tonnen Roheisen
Der übliche Hochofen hat in der Regel eine Höhe von etwa 25 bis 30 Metern
Der Ofen besteht aus feuerfesten Steinen, welche von einem Stahlmantel umfasst werden
Die Aussenwand eines Hochofens wird permanent durch geschlossene Kühlkreisläufe gekühlt
Benötigte Rohstoffe zur Produktion von Roheisen:
Eisenerze
Koks
Kohle
Öl
Gas
Kalk
Luft und reinen Sauerstoff
Im Hochofenprozess werden Eisenerz, Zuschläge und Koks von oben in den Hochofen eingebracht. Die Hitze im Hochofen führt dazu, dass der Koks den Sauerstoff bindet und unerwünschte Verunreinigungen teilweise durch die Schlacke abgeführt werden.
Um den Hochofenprozess aufrechtzuerhalten, erfolgt die Zufuhr von heisser Luft, die als «Wind» bezeichnet wird, in den unteren Teil des Ofens. Bevor der Wind in den Ofen eingeblasen wird, erfolgt eine Vorwärmung in den Winderhitzern (Cowper), um die gewünschte Betriebstemperatur zu erreichen.
Materialbilanz für die Herstellung von 12 000 Tonnen Roheisen. Dies entspricht einer durchschnittlichen Tagesproduktion eines modernen Hochofens.
Zufuhr in die Hochöfen:
Material | Gewicht |
---|---|
Erz und Zuschläge | 19 200 Tonnen |
Koks | 3 600 Tonnen |
Kohle | 2 160 Tonnen |
Heisswind | 10.8 Millionen m³ |
Sauerstoff | 1.2 Millionen m³t |
Abgeführt werden:
Material | Gewicht |
---|---|
Roheisen | 12 000 Tonnen |
Schlacke | 3120 Tonnen |
Gichtgas | 16.8 Millionen m³ |
Staub | 12 Tonnen |
Beim Abstich am Hochofen wird der geschmolzene Inhalt des Ofens durch eine verschlossene Öffnung am unteren Teil entnommen. In der Abstichhalle wird der austretende Inhalt mithilfe eines Rinnensystems in Schlacke und flüssiges Eisen getrennt. Die meisten Hochöfen verfügen über zwei separate Abstichvorrichtungen: eine für die Schlacke und eine etwas tiefer liegende für das flüssige Eisen. Dabei wird der Unterschied in der Dichte genutzt, um eine effiziente Trennung zu ermöglichen.
Schlacke ist ein Gemisch aus verschiedenen Oxiden wie Siliziumoxid (Kieselsäure, Silikat) Calciumoxid, Magnesiumoxid, Aluminiumoxid (Tonerde) und weitere . Normalerweise wird sie vereinfacht als Calcium-Aluminium-Silikat beschrieben. Diese Schlacke wird oft in Form von groben Partikeln oder granuliertem Hüttensand verwendet und findet auch in der Technik Anwendung. Silikatische Schlacken werden weiterhin zu Stein- und Schlackenwolle verarbeitet.
Vom Hochofen ins Stahlwerk
Das im Hochofen gewonnene Roheisen ist noch weit entfernt von einem technisch nutzbaren Stahl. Roheisen enthält 4 bis 4.7 % Kohlenstoff und weitere reduzierte Elemente wie Schwefel, Phosphor, Silizium und Mangan.
Das Roheisen wird nach dem Abstich in Torpedopfannen abgefüllt und über das werkseigene Schienennetz ins Stahlwerk gebracht. Dort wird das Roheisen in Konvertern zum eigentlichen Stahl umgewandelt (konvertiert). Hierbei werden ihm unerwünschte Eisenbegleiter, Verunreinigungen wie Schwefel, Phosphor, Silizium, Kohlenstoff und Mangan, weitgehend entzogen.
Roheisen-Behandlung in der Torpedopfanne
Die Roheisen-Behandlung ist ein entscheidender Schritt im Stahlherstellungsprozess. Sie beginnt teilweise bereits in der Torpedopfanne mit einer Entschwefelung.
Auf die wichtigsten Prozesse im Konverter hin zum Rohstahl werfen wir im Folgenden einen genaueren Blick:
Entschwefelung: Schwefel ist eine Verunreinigung im Roheisen, die die Qualität des Endprodukts beeinträchtigen kann. Um Schwefel zu entfernen, wird ein Entschwefelungsmittel wie Calciumcarbid, Magnesium oder Natriumcarbonat (Soda) in die Torpedopfanne eingeblasen. Diese Materialien reagieren mit dem Schwefel im Roheisen und bilden Schlacken, die leichter sind als das flüssige Eisen und daher abgeschieden werden können. Die Entschwefelung verbessert die Schweissbarkeit und die mechanischen Eigenschaften des späteren Stahls.
Entphosphorung: Phosphor ist eine weitere Verunreinigung, die aus dem Roheisen entfernt werden muss, da hohe Phosphorgehalte die Stahlqualität beeinträchtigen können. Kalkhaltige Flussmittel, die Calciumoxid (Kalk) enthalten, werden zugesetzt, um den Phosphor im Roheisen in Form von Phosphorschlacke zu binden. Diese Schlacke steigt an die Oberfläche des flüssigen Eisens auf und kann leicht abgeschöpft werden.
Entsilizierung: Silizium ist eine Verunreinigung, die in Roheisen vorhanden sein kann und die Schweissbarkeit und Festigkeit des Stahls beeinträchtigen kann. Eisenoxid oder andere siliziumreduzierende Mittel werden zugesetzt, um das Silizium zu oxidieren und in die Schlacke zu überführen. Dies erleichtert die Entfernung des Siliziums aus dem flüssigen Eisen.
Entkohlung: Durch Einblasen von reinem Sauerstoff wird der Kohlenstoff verbrannt. Bei diesem als “Frischen” bekannten Vorgang erhitzt sich die Schmelze stark und schnell (exotherme Reaktion). Um eine übermässige Erhitzung zu vermeiden, wird Stahlschrott zur Kühlung eingesetzt.
Desoxidation: Durch das Frischen erhöht sich der Sauerstoffgehalt in der Schmelze, was ebenfalls unerwünscht ist. Dieser wird mittels Desoxidation mit Silizium oder Aluminium wieder gebunden und über die Schlacke abgeführt.
Die Roheisen-Behandlung erfordert präzise Kontrolle und Überwachung, um sicherzustellen, dass die Verunreinigungen auf das gewünschte Niveau reduziert werden.
Am Ende der Roheisenbehandlung im Konverter liegen Rohstahl-Chargen vor mit definierten Gehalten an Kohlenstoff, Silizium, Mangan, Schwefel, Phosphor und Sauerstoff.
Der Rohstahl wird nun über weitere metallurgische Prozesse so behandelt und legiert, dass ein Stahl mit definierter chemischer Zusammensetzung und dem gewünschten Eigenschaftsprofil vorliegt.
Es ist wichtig zu betonen, dass Rohstahl nicht mit Edelstahl identisch ist. Rohstahl dient als Ausgangsmaterial und muss weiteren Verarbeitungsschritten unterzogen werden. Edelstahl rostfrei enthält mindestens 10,5 % Chrom (Cr) und bis zu 1,2 % Kohlenstoff (C).
Lesen Sie auch unseren Blog «Die Rostfrei-Revolution - Eine faszinierende Reise durch die Welt des nichtrostenden Stahls»
Der Übergang von Rohstahl zu Edelstahl erfolgt durch Zugabe von den beschriebenen Legierungselementen und speziellen Verarbeitungsverfahren, die den Stahl veredeln.
Erkenntnisse
In dieser Erkundung des Herstellungsprozesses von Rohstahl haben wir einen Einblick in die Welt der Metallurgie erhalten. Vom Abbau der Erze bis zur Umwandlung in Rohstahl wurden die komplexen Schritte und Technologien hinter dieser lebenswichtigen Industrie beleuchtet. Wir haben gesehen, wie modernste Verfahren und Technologien dazu beitragen, die Qualität und Effizienz der Stahlherstellung ständig zu verbessern.
Abschliessend können wir festhalten, dass Stahl mehr als nur ein Baustoff ist. Es ist ein Symbol für Fortschritt, Innovation und die Fähigkeit des Menschen, seine Umwelt zu gestalten.
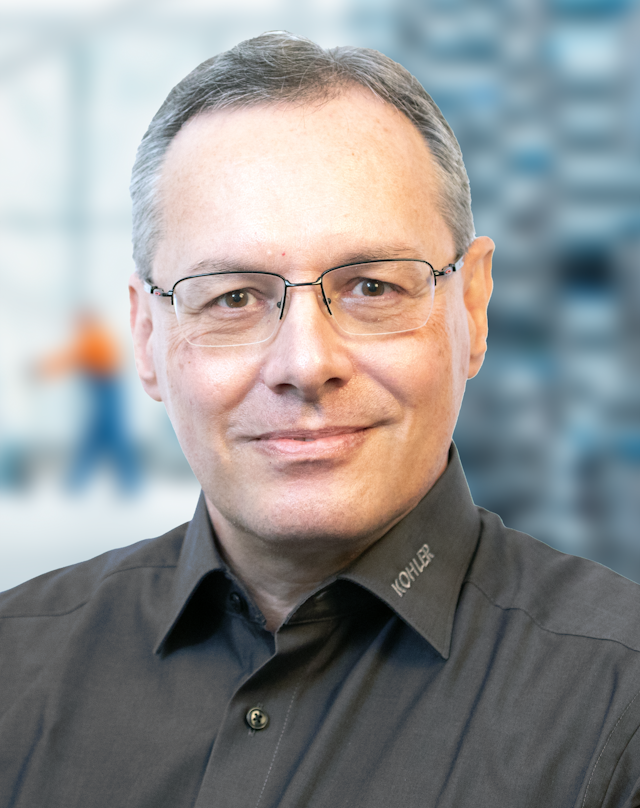
Haben Sie Fragen? Ich berate Sie gerne!
Kontakt
Dr. René Mächler
Leiter Qualitätsmanagement & Technik / Dipl. Werkstoffingenieur ETH
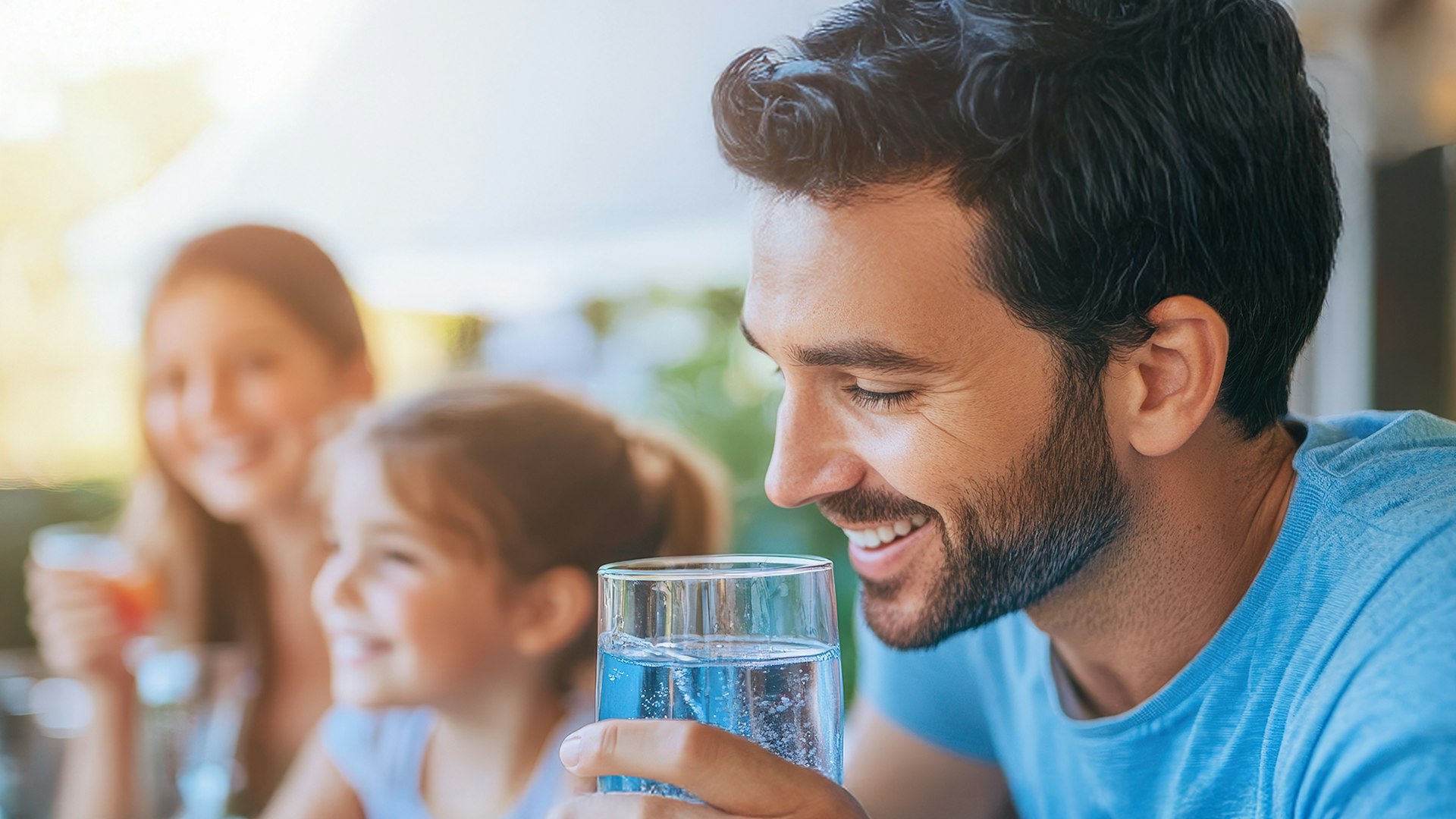
- Fachwissen
- Anwendungsbeispiel
- Referenzen
- Beratung
Alles über das Projekt «Erweiterung ARA Basel» zur Verbesserung der Abwasserreinigung
Die Abwasserreinigungsanlagen und Edelstahl sind eine unverzichtbare Kombination, um Trinkwasser in einer hohen Qualität der Bevölkerung bereitzustellen.

Sinnstiftende Partnerschaften: KOHLER fördert Sport, Innovation und Wissenschaft
KOHLER legt grossen Wert darauf, bedeutsame Aktivitäten zu fördern und sich in einem engagierten Netzwerk als aktive Playerin zu positionieren.
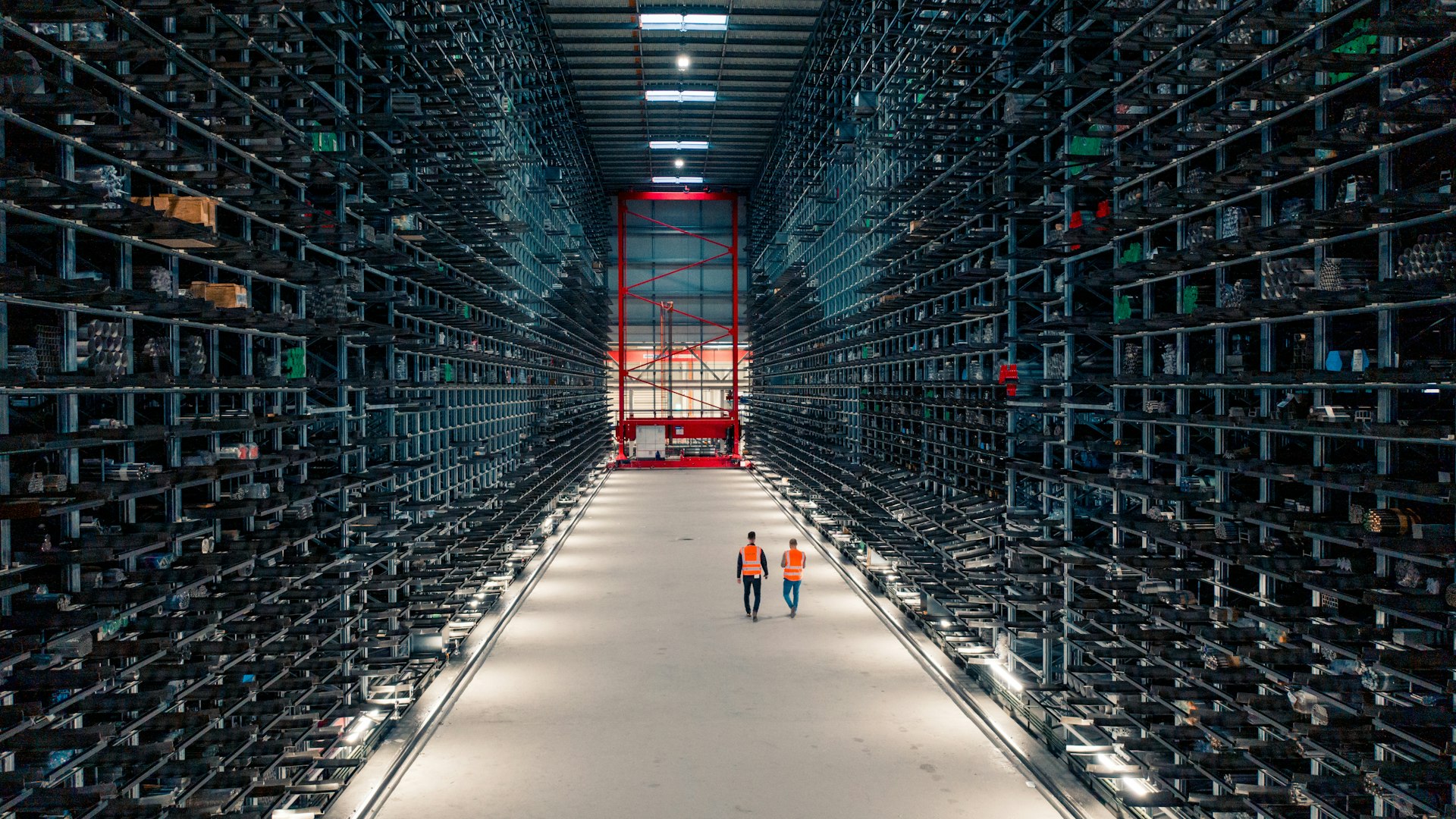
HANS KOHLER AG - Ihre Nr. 1 für Edelstahl
Die HANS KOHLER AG ist eine eigenständige, unabhängige Handelsunternehmung mit Sitz in Zürich.